HRSG, valve issues addressed during major overhaul; M&D added to GTs, transformers
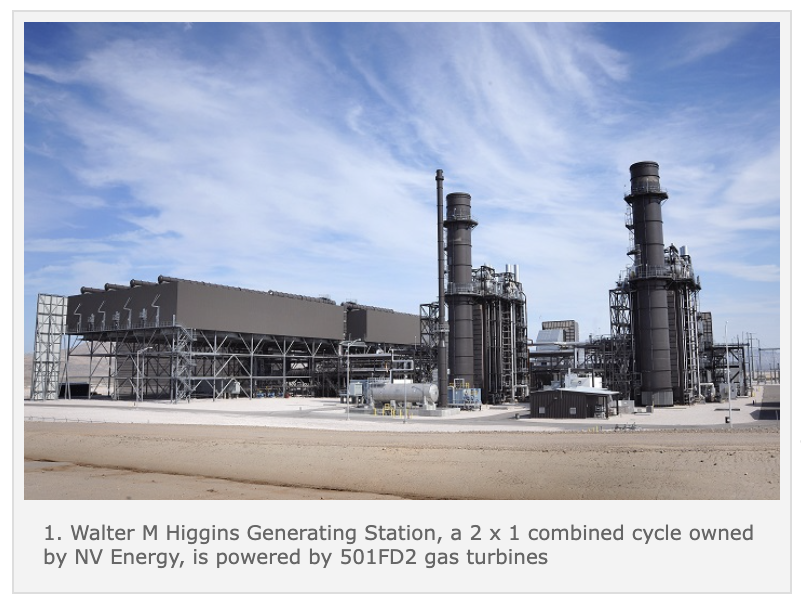
NV Energy had the luxury of time for the first gas-turbine major inspection at its Walter M Higgins Generating Station, located in Primm, Nev, near the California border about 40 miles southwest of Las Vegas (Fig 1). With demand still down from pre-recession levels, the company conducted the outage when temperatures were moderate, from February to May, thereby avoiding the overtime and premium services normally associated with a major. This was the only GT major conducted by the utility in 2013.
Higgins is a 2 x 1 combined cycle powered by 501FD2 gas turbines from Siemens Energy Inc. The air-cooled plant began commercial operation in 1Q/2004 as Bighorn Generating Station, then owned by Reliant Energy Inc. Higgins has compiled some enviable statistics over the years, most recently 100% starting reliability in 2012: 131 starts in as many attempts.
The outage involved work on the gas turbines, steam turbine, heat-recovery steam generators (HRSGs), high-energy piping, air-cooled condensers, SCR and oxidation catalyst beds, battery banks, critical instrumentation, etc. The editors participated in a roundtable discussion with several NV Energy engineers who played a significant role in the various projects conducted—including Josh Langdon, Jimmy Daghlian, Christian Herrera, Scott Amos, and Alex Fitzgerrells. Goal was to gather information for the following outage profile, which focuses on the inspections conducted, corrective action taken, and improvements made.
GAS TURBINES
A major concern of the utility’s engineers was the integrity of compressor thru bolts, which had failed on two units in the 501F fleet during 2012. Removal of the rotor, as required for the major inspection, exposed the forward ends of the 12 bolts and nuts between the second and third compressor stages (Fig 2), facilitating the recommended UT inspection. Siemens inspected each rotor (about a day per unit) and found no indications.
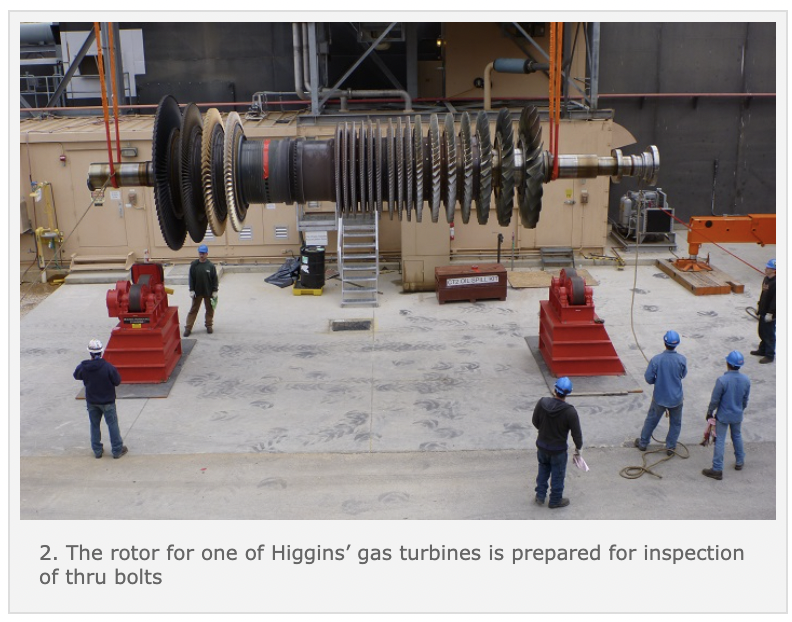
PSM, which was conducting the GT overhaul as the third-party LTSA provider, in conjunction with inspection experts from Advanced Turbine Support LLC, provided a second opinion on bolt health. They identified two indications on one unit; however, those anomalies were smaller than the minimum size of concern established by Siemens.
Turbine Row 1 and 2 ring segments and blades had slightly more than 24,000 equivalent service hours and were replaced with like components manufactured by PSM. There were no major findings in Rows 3 and 4, but “heavy” repairs were required to correct for creep. R3 vane deflection, a fleet issue, also was addressed.
The No. 1 bearing on each unit was rebabbitted to correct for general wiping. There also was uniform wear of the thrust bearing but no scoring. It too was rebabbitted. A check of the exhaust section revealed wear and tear similar to that experienced by others. There was some cracking on the diffuser and that was weld-repaired after reassembly of the exhaust case. Engineers said that the plant’s proactive preventive maintenance program for the exhaust section has been effective in minimizing the need for major repairs. Struts were in acceptable condition and no bearing drop was in evidence.
Combustion section hardware—fuel nozzles, transition pieces, baskets, support housing—had been replaced in January 2012 with PSM 12K components and they were in good condition.
A white deposit was found on flow-path components from the compressor inlet through to the turbine section. This was caused by a process upset in the evap cooler that allowed off-spec makeup into the unit for about 24 hours. The fouled media was replaced and a root-cause-analysis (RCA) investigation was being conducted at the time of the editors’ visit to Higgins to assure this would not happen again.
NV Energy installed PSM’s Combustion Autotune System on one of the Higgins GTs to automatically optimize combustion dynamics and emissions, holding both within specified limits while compensating for variations in ambient conditions, fuel-gas composition, and engine deterioration. This eliminates the need for seasonal tuning. This is the first application of Autotune on a 501F series engine. It is installed and is meeting expectations on several GE 7FAs—including units with Mark V, Ve, VI, and VIe control systems. One of the immediate benefits of the system was a reduction in ammonia consumption for NOx control.
The Higgins gas turbines were reassembled without incident.
HEAT-RECOVERY STEAM GENERATORS
NV Energy has invested in training staff engineers over the last several years to conduct HRSG inspections in-house. Attendance at the HRST Inc’s HRSG Academy [link] and participation in inspections conducted by outside experts have underpinned staff education. The utility’s engineers are well versed in where to look and what to look for during inspections. Plus, they have access to prior inspection reports, so they know going into a given unit what the previous issues were and where to pay special attention.
The Higgins HRSG inspection was conducted by two engineers and took a full seven days. Tools of the trade: flashlights, mirrors, wire brushes, etc. Contractors are called in when a second opinion is necessary or special nondestructive examination (NDE) is required. The inspectors checked penthouse, vestibules, HP/IP/LP drums, stack, etc, looking for loose components (such as chevron steam separators), indications on belly pans, checking oxide colors in drums, cracking in downcomer welds, etc.
Indications were found in downcomer welds and Structural Integrity Associates (SIA) was called in; their inspectors found no cracking. A borescope used to inspect downcomers and risers on the LP evap section identified minor flow-accelerated corrosion at bends. It wasn’t a serious condition; merely tracking. The lower IP and LP headers, made of carbon steel, showed no trace of FAC.
Some indications were found on the HP economizer and HP evaporator at the lower header-to- tube joints. NDE follow-up gave no cause for concern. Some tube rows were inspected full-length. Impact damage between bumpers and scallop bars were corrected by repositioning the bumpers with a slight offset. To protect the tubes against scallop-bar rub wear, sleeves were installed on tubes where the scallop bars are located. The traditional industry fix of welding together two hemispherical tube shields was used.
Some superheater tube rows immediately downstream of the duct burners revealed overheating damage: The metal decarburized and failed. SIA checked hardness and microstructure of tubes (T91, 1.5 in. diam, 200 mils minimum wall) in the region of interest and recommended replacement of 94. A lot of science went into the analysis and decision-making to hold costs in check. Original tubes were cut out leaving stubs in the top and bottom headers and new tube material was welded to those stubs. Welds were checked using linear phased array. Utility engineers surmised that the metal damage was caused by overfiring in periods of peak demand before NV Energy bought the plant.
Visual inspection of socket welds in HP economizer drains revealed the likelihood of improper fit-up and poor weld quality. More than 100 welds were repaired. A squeeze hydro was planned the week before restart to check for leaks and allow use of the same water for plant restart.
The reheat-steam attemperator installed at Higgins was not equipped with a liner, which is standard in all plants built by the utility. By contrast, the HP superheater attemperators had liners. The spool pieces for the reheat-steam attemperators, about 10 ft long x 18 in. diam, were replaced with ones having liners. A metallurgical assessment revealed welds, pipe, and headers downstream of the spool pieces were in satisfactory condition.
VALVES
The roundtable discussion moved from HRSGs to large steam valves. It focused on stellite liberation from high-pressure (HP) and hot reheat (HRH) valves serving in F-class combined cycles. Tight shutoff of parallel-slide gate and non-return globe valves has been compromised in some cases. This is an industry-wide problem and something NV Energy is dealing with at Higgins and other plants. The company’s experience was factored into the industry roundup published earlier.
GENERATORS
GT generators. The Higgins gas turbines are coupled to Siemens Aeropac totally enclosed water-to-air cooled (TEWAC) generators, each rated 209 MVA at 18 kVand 0.85 power factor. A borescope inspection was conducted during the major to look for possible spark erosion. This was the second such inspection since a full rewind in March 2010 to verify that the new ripple-style slot filler had eliminated the spark erosion experienced with the original windings.
NV Energy engineers pointed out that not all available ripple fillers are capable of operation at the temperatures expected in the Higgins machines, nor are all capable of applying the force required given the available space in the slot. The ripple fillers installed in 2010 were specifically qualified for use in the Aeropac machine.
The straight portions of the coils in the slots were inspected using an articulating borescope through the radial vent slots in the core, from the outer diameter. Two rings of vent slots were inspected, one on the turbine end and one on the collector end. One half ring also was inspected in the top center of the core.
The inspection revealed no indications consistent with the appearance of spark erosion or partial discharge. Slot images were reviewed by the engineering department, which confirmed the conclusions drawn by inspectors. Validation of the rewind solution means no additional borescope inspections are required.
ST generator. A diagnostic inspection with rotor in-situ (DIRIS) was conducted on the Alstom hydrogen-cooled generator for the steam turbine, rated 391 MVA at 21 kV and 0.85 power factor. This robotic inspection focused on stator wedge tightness and core integrity. In addition, the generator inspection program included review of the complete machine and its auxiliary systems, rotor-winding condition, stator/rotor winding polarization index, leakage-current HV testing, and a low-flux iron stator core test.
Inspection/test results met expectations. The slot wedge assessment met OEM criteria, the low-flux core iron test revealed no critical interlamination shorts, and no specific rotor winding issues were detected. Additionally, modal/impact testing was performed on the end windings. That effort indicated the elliptical (N=2) mode shapes of both baskets remained “low tuned”—below the 120-Hz excitation frequency. Thus there will be no vibratory amplification of the elliptical (N=2) ring modes. End-winding vibration is consistent with a 30-yr generator lifetime.
Local response testing showed that the local end-turn response amplitudes were below the acceptance criteria (less than 0.05 g/lb) with no concern about local independent resonances. Testing of the phase leads also revealed all responses were below 0.05 g/lb and no concern regarding local independent resonances.
Vibration of the generator frame and foundation are of continuing concern but the implementation of mitigation procedures has reduced the significance of the issue. Example: Vibration-induced instrumentation problems of the past generally have been eliminated. Vibration was conducive to the cracking of some external pipes, but they have been fixed and their support systems improved. Loosening of internal fasteners was identified; problem solved by replacing conventional washers with Nord-Lock washers. The OEM told plant personnel the only way to eliminate any lingering vibration problems is to replace the generator, which it has done on two of the four units equipped with the same generator installed at Higgins.
TRANSFORMERS
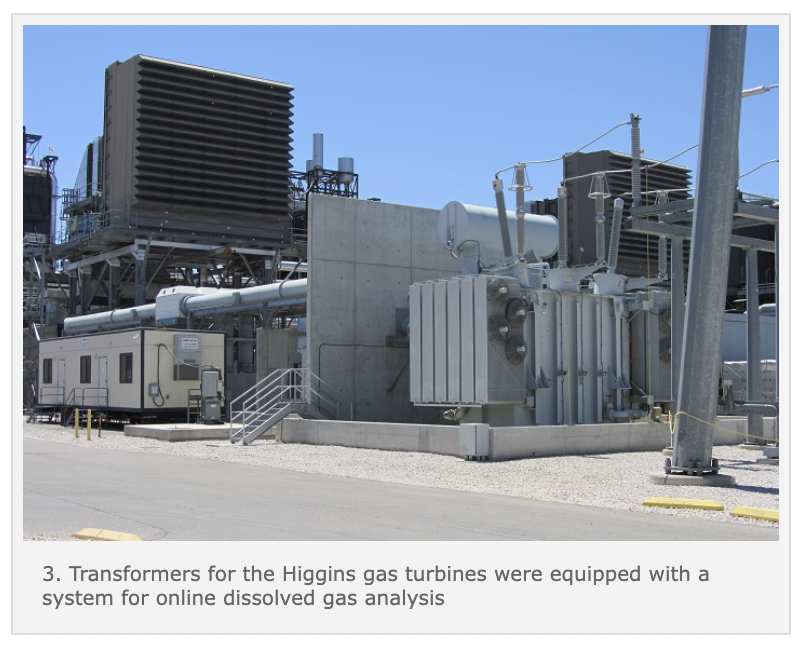
Higgins invested in a dissolved gas monitor for its transformers to help detect impending fault conditions and prevent lengthy forced outages (Fig 3). DGA, or dissolved gas analysis, is considered the single most powerful tool for transformer fault detection and asset management.
An eight-gas (H2, CO, CO2, O2, methane, ethane, ethylene, acetylene) online DGA monitoring unit from Kelman Ltd was installed during the outage. It relies on advanced photo-acoustic technology to measure all significant fault gases, plus moisture in oil, without need for carrier or calibration gas. Data from the gas analysis go to the plant DCS (TXP) and are stored in PI on a 1-sec basis.
The plant also installed Doble Engineering Co’s online intelligent diagnostic device (IDD) to continually monitor bushings and current transformers (CTs). The system detects abnormalities in the insulation system and, when appropriate, issues alerts—both locally and remotely. This keeps asset managers informed about the status of their bushings and provides the lead time necessary to determine appropriate corrective action, if necessary.
When IDD identifies abnormal bushing behavior it analyzes leakage current and assesses the condition of the insulation system. More specifically, IDD calculates the absolute and rate-of-change of power/dissipation factor and capacitance of the problem bushing, enabling it to determine the severity of the problem. Advanced signal processing and field-proven algorithms are designed to eliminate noise effects and other environmental conditions conducive to incorrect diagnosis and inappropriate corrective action. CCJ