Tenaska Virginia Generating Station’s (TVGS) prominent and ongoing participation in the CCJ Best Practices Awards program over the last 10 years (Sidebar 1) is as much about technical and equipment improvements (Sidebar 2) as it is about employee and community relations. But it is with the latter that the facility has imprinted an indelible mark of leadership for the electric-power industry.
Plant Manager Dr Robert Mayfield responded to the editors queries regarding earlier Best Practices with the following update, which can be summarized this way: Nurturing your roots means taking care of your employees—your ambassadors—while implementing programs with significant impact, along with meaningful actions which establish personal relationships.
Mayfield’s “triple bottom line,” a sustainability concept combining people, community, and the environment, continues through all-voluntary actions. During holidays, employees and spouses donate their time and money shopping for toys (Fig 1), clothing, and Easter baskets (Fig 2) for at least 100 children and elderly in the county. The company matches monetary contributions.
Year-round, employees donate to the local food bank, sponsor one church food drive per quarter (feeding at least 500 guests), and offer math tutoring, reading, science expo judging, facility tours, spelling bees and career fairs for area schools.
In the meaningful actions category, TVGS employees supported a home for elderly unwanted dogs, donated to build a house through Habitat for Humanity, provided 50 reading books for a sixth-grade English class, supported high-school agriculture, science-fair (Fig 3), and art (Fig 4) programs, added TV and audio booms for a high school, and sponsored a back-to-school luncheon for teachers.
Recent activities identified through the eco-environmental program include collecting 400 used cell phones and accessories for an AT&T sponsored program called Cell Phones for Soldiers, collecting newspapers and aluminum cans for the Boy Scouts recycling program, providing environmentally friendly foam cups, and copying paper on two sides to reduce consumption.
Keeping ambassadors safe, content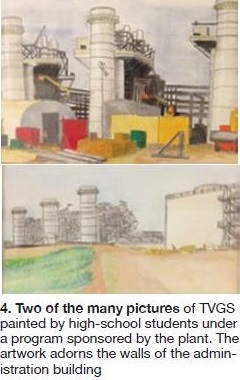
TVGS conducts a “safety toolbox” meeting every Wednesday during outages to discuss such items as scaffolding and opportunities for improvement in processes. Contractor supervisors discuss major maintenance activities for the week. Extensive audits are conducted for lock out/tag out (LOTO) procedures, which then guide pre-and post-outage training for improvement.
Through strategic engagement, plant personnel are encouraged to propose new ideas for employee relations. As a result, TVGS now sponsors fun and recreational activities like a casino night, rafting and canoeing on the Rivanna River, summer barbeque, annual party for employee children (a bowling party in 2013, a swimming party in 2014), daily bingo numbers for gifts, and an outage barbeque for all outage contractors and workers onsite.
The TVGS Safety Committee conducts detailed reviews of work process controls, permits, LOTO, confined-space, and hot-work policies. Mayfield reports the plant is on Revision 18 of its work permits, which include fall protection, trenching, and scaffolding. Work-permit documents are color-coded to help workers identify them. All procedures are reviewed and updated annually as part of safety continuous process improvement.
Staying online
Nothing enhances employee and community relations as much as superior performance. TVGS has been challenged in recent years by brutal winter storms (Fig 5). Cold-weather preparation has therefore become part of continuous improvement. Volunteers remain onsite during bad weather events.
Staff monitors the weather and radar maps to stay ahead of an approaching storm. Food is purchased in advance and cots and bedding are stowed for emergencies. Heat tracing is monitored continuously, and the plant has added heated sheds around critical equipment exposed to freeze conditions. Staff uses the fall outage to prepare and train for winter operations. Finally, TVGS reviews all corporate fleet lessons learned, best practices, and event reports for winterization. CCJ
1. TVGS an industry leader in best practices
The Best Practices Awards program for owners and operators of generating facilities powered by gas turbines, sponsored by the CCJ with widespread industry support, celebrates its 10th anniversary in 2014. To commemorate the occasion, the editors are recognizing the plant staffs that have shared most generously the technology, procedures, and ideas they have used to assure top performance on a predictable and repeatable basis while minimizing emissions and maintaining a safe working environment.
There are two levels of awards to recognize the achievements at individual plants: Best Practices and The Best of the Best, as voted by a team of highly experienced judges. Tenaska Virginia Generating Station is one of five facilities receiving special recognition. The plant earned a total of 20 awards during the program’s first decade (list below).
Its success, and that of the four other generating facilities—Tenaska Lindsay Hill, Tenaska Central Alabama, Effingham County Power, and Klamath Cogeneration Plant—reflects a commitment to sharing by very capable management teams that have been in place since COD, in most cases. Continuity of ownership, and an executive corps with deep experience in plant engineering and operations, also contributed significantly to the success of the facilities recognized.
Best of the Best Awards
2014 Workforce Development
2010 Safety
2007 Operation & Maintenance
2006 Management
Best Practices Awards
2014 Outage Management
Performance Improvement
2012 Operation & Maintenance
2011 Management
Operation & Maintenance
2010 Management
Operation & Maintenance
2009 Safety
2008 Environmental Stewardship
Management
Operation and Maintenance
2007 Management
Operation & Maintenance (2)
2006 Operation & Maintenance
Management
2. Learn from TVGS’ critical technical, hardware BPs, too
Good ideas are timeless. For those new to the industry, or those who missed the first reports, the editors have summarized below TVGS’s most popular best practices from the last 10 years. For more detail, simply click on the link of interest.
BP 1. Plant personnel made work conditions in the gas-turbine compartment safer by improving lighting and access to power tools. Transformers rated 480/240 V were installed in each turbine electrical control building, with conduit to a 50-amp receptacle. Modular skids can be connected as necessary. Light strings with magnetic plates made installation and modification of temporary lighting simple and convenient for workers to have light where needed. Read more. . . .
BP 2. The safety committee reviews plant ergonomics quarterly, and an occupational therapist provides training to avoid ergonomic-related safety hazards. The program goes beyond just desk and computer-related posture, addressing movements like crawling in and out of HRSGs, heavy lifting, and repetitive tasks common to an industrial environment. Read more. . . .
BP 3. A Six Steps for Continuous Improvement approach was implemented to avoid HMI (human machine interface) failures caused chiefly by hard drives and power supplies. A simple continuous improvement approach based on define/measure/improve was used to manage excessive boiler-feedpump failures. Continuous improvement is a company “core value.” Read more. . . .
BP 4. TVGS implemented a program to obtain buy-in from onsite contracted employees to the plant’s safety culture. Contractors are invited to participate in regularly scheduled safety meetings, must sign the plant’s safety charter, collaborate to review best methods for job execution, and are free to offer their feedback and concerns. Read more. . . .
BP 5. Many of the activities and most of the results reported here fall under a customer-centric philosophy at the plant that shifts business practices from what we do to who we serve, “who” being the customers or stakeholders—employees, contractors, partners, and community members—as well as the obvious customers of the electricity product output. Read more. . . .
BP 6. TVGS developed and maintains an intranet-based, fleet-wide knowledge management system designed to capture staff “tacit knowledge,” knowledge which isn’t explicit (that is, articulated in a set of procedures or documents) but is based on experience, intuition, etc. Read more. . . .
BP 7. TVGS staff developed a means of responding in real time to Automated Generation Control (AGC) dispatches, which change every five minutes. This required new logic to optimize among the gas and steam turbine outputs, the duct burners, etc, as well as revamping how the GT and duct-burner controls interact with the DCS. Read more. . . .