Repair of tube leaks: The good, the bad, the ugly
All owner/operators of combined-cycle and cogeneration plants will tell you they “want a good job,” especially when it comes to the repair of boiler pressure parts—tubes, for example (Fig 1). However, many do not realize that job quality depends in large measure on their involvement in the repair project.
The starting point is contractor selection, Bill Kitterman and Bob Morse of Bremco Inc, Newport, NH, told attendees at a recent Combined Cycle Roundtable sponsored by the Combustion Turbine Operations Technical Forum (CTOTF). Price is very important, but it’s not everything, the repair experts advised. If your due diligence of alternative service providers is incomplete and you hire a contractor without the specific capabilities required to ensure project success, they continued, your expectations may not be achieved.
Kitterman had presented in detail on “How to select the right contractors to support your next outage” at an earlier Frame 6 Users Group meeting. You can obtain a summary of his remarks before that forum by accessing the 3Q/2006 issue at www.ccj-online.com.
The plant’s responsibility doesn’t end with contractor selection, Morse said. One or more members of the owner’s O&M team should be assigned to follow the project and ensure that the work being done satisfies the company’s requirements. Kitterman flashed samples of ugly work up on the screen (Figs 2, 3), noting that just because the weld holds a hydro doesn’t mean it was done correctly. The backside weld shown in Fig 4 illustrates the “good” workmanship most owners expect.
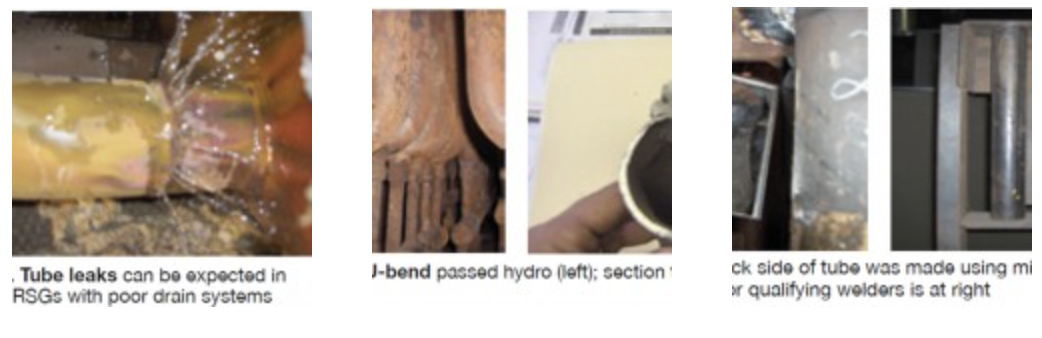
Plant staff should prepare for a contractor’s visit with a thorough review of the job plan, weld procedures including QC hold points, and welder qualifications. Kitterman suggested obtaining the continuity logs for welders. It’s important to verify is that each welder has struck an arc within six months of your project’s start using the process/procedure required for your work—a Code requirement. Continual practice is required; perfection can be illusive. The mirror test jig in Fig 5 is used for both practice and welder qualification.
Closeout paperwork provides a complete record of the job and is extremely important to obtain and retain. The package should include detailed work procedures followed, welder qualifications, identification of welders for specified, materials receipt and test reports, QC documentation, drawings, copies of official reports on code work, safety record, cost, etc.
Much of this information is included in the “Form R-1 Report of Repair” provided in accordance with provisions of the National Board Inspection Code (NBIC). More is recorded in the so-called “Job Traveler,” which describes major project activities—final visual inspection, for example—and the names of the contractor’s QC inspector and NBIC Authorized Inspector (AI) signing off on each.
Planning the job
Kitterman and Morse spent most of their time at the front of the room walking users through typical pressure-parts repair activities, to prepare them for the types of work that would be done in their plants and decisions they might be involved in. Regarding decisions, consider the following:
- When a leak occurs, do you take the unit out of service or continue to run?
- How do you “fix” the damage: patch, repair, replace?
- What type of weld repairs do you want in your boiler?
- Should you perform NDE beyond that required by the Code—such as sample analysis?
Tube-to-header weld designs were first on the list of discussion items. If you’re involved in developing specifications for replacement tube panels or repairs required for a replacement harp, you have to speak the same language as the fabricator or contractor. Terms you should be familiar with are bulleted below. At this point in the presentation, Morse banged the company drum for a minute. In over a decade of repair work on HRSGs ranging from aero to F-class sizes, he said, Bremco has never had to plug a tube.
- Stick-through with standard “J” bevel is the most common tube-to-header joint configuration because it meets the HRSG designer’s performance requirement and is the least expensive weld joint for panels. The fillet weld used does not require the higher level of skill that an open-root weld demands, so you can expect consistent top quality for these joints from experienced welders.
- Stick-through with contoured weld groove is very similar to the standard “J” bevel design, but by articulating the “J” bevel around the hole contour a weld groove of constant depth is achieved on both the high and low sides of the header tube hole. It can require more filler metal than the standard “J” around the low side of the joint, depending on the weld technique, but the additional welding generally is negligible.
- Socket seat is often used in upper headers because the design facilitates draining. This is not to say that other joint configurations cannot be made to drain as efficiently. If both upper and lower headers are specified with this joint, additional trim-to-fit labor normally is required.
- Set-on configuration uses a header tube-hole diameter equal to or smaller than the tube ID. This joint requires an open-root weld and the back side is inaccessible; therefore, it demands a higher degree of skill from the welder than is required for most other joint configurations.
- Spot-face set-on, similar to the set-on, eliminates the need to fish-mouth the tube end by spot-facing the header. This also is an open-root weld, but the recess can make for more difficult access to the root. It may require double the welding labor than that required for the simple set-on joint.
- Extruded-header tube holes enable butt-welding of tubes to the header. If both upper and lower headers are of the extruded design, additional trimming of tubes typically is required during tube fit-up. This can be avoided by designing the lower header with stick-through joints. Additionally, this joint uses an open-root butt weld, which requires greater skill on the part of the welder than some of the other joints shown.

Find the leak. If you the owner/operator finds the leak, your company will reduce the cost of repairs. Pinpointing the leak location for the contractor—such as, section of unit, upper or lower half of the boiler (or elsewhere), at a tube-to-header weld or not, header location (in a bundle or in the open)—facilitates job planning and execution.
Selecting the optimal repair method is next. Depending on where the leak is located, access may require raising or lowering one or more panels, or jacking apart the panel with the leaker and the harp next to it. It might be expeditious to cut your way in and weld your way out, but be sure the necessary amount of tube stock is on hand. Tube plugging is another option to consider. Tube material (T91, T22, T11, carbon steel) will impact the repair process; know what’s in your HRSG and where.
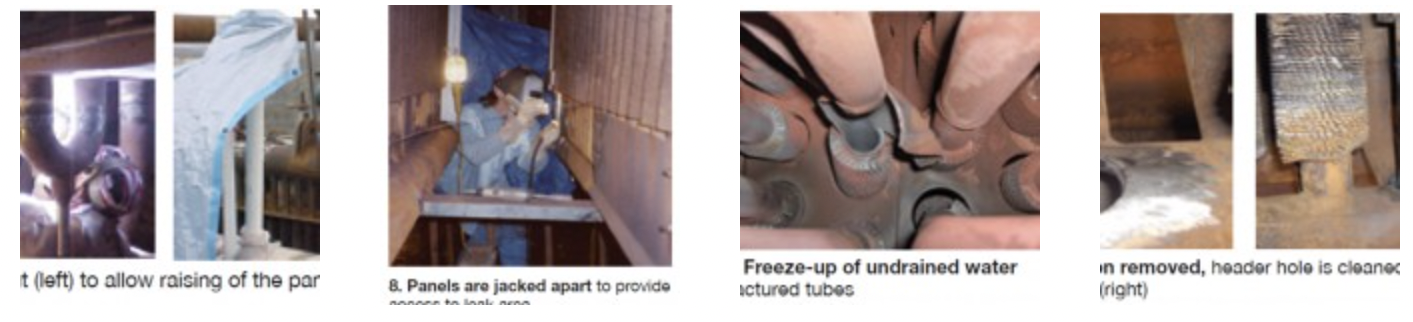
Raising (or lowering) a panel to make repairs demands experience (Fig 6). The task must be carefully thought out to minimize the number of steps and assure a safe work environment. It typically includes cutting of jumper piping (Fig 7), drains, etc; use of restraints to hold the repositioned harp in place while work is done; stress relief; rigging. Jacking of panels also involves cutting restraints and drains and requires proper blocking (Fig 8).
Tube leaks typically are traced to flow-accelerated corrosion, rapid quenching of hot tubes caused by improper operation of header drains during startup or leaking attemperators, etc—even freeze-up of undrained water (Fig 9). The majority of tube leaks is located near the upper or lower header and the typical fix is to cut out the damaged material, dress the header penetration (Fig 10), weld-prep the open end of the remaining section of tube, and weld in a stub (Fig 11).
At first glance, it would appear that all this effort could be saved by tube plugging. But plugging is not as simple as it sounds. Kitterman and Morse said this was the least-desirable solution in their minds, one involving strong Code involvement and a high level of skill (Fig 12). In all probability, stress relief of affected headers will be required.
Plugging a tube requires cutting into the top header to install the plug. Repairing the header after the plug is set requires cutting material from a new header to serve as the patch. The patch is cut out slightly oversize and fit-up is accomplished by grinding off the heat-affected zone. The header must be stress-relieved after the patch is welded in place. A good patch is shown in Fig 13, a bad patch (square with sharp corners that cause stress risers) is illustrated in Fig 14, and an ugly arrangement of two square patches side by side, with a generous supply of weld bead, presented in Fig 15.
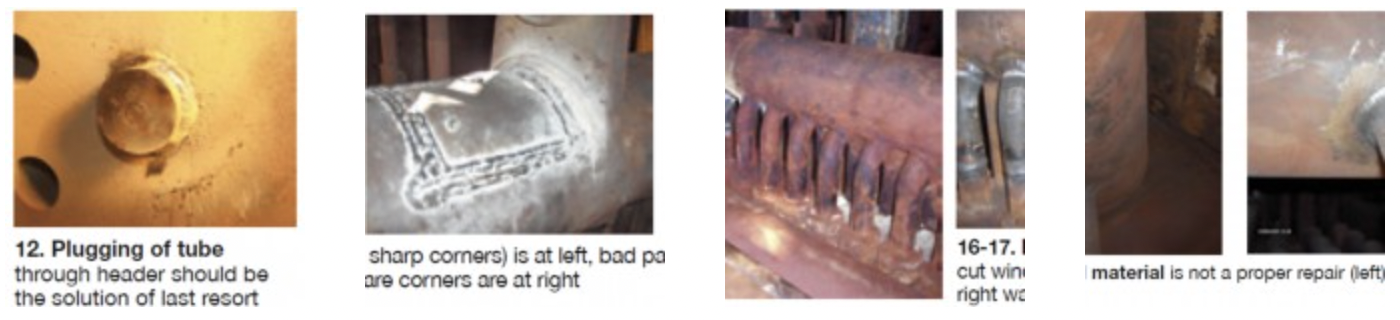
All repairs must be made according to one or more codes, Kitterman continued. “Code” is not just another four-letter word, he said, it’s the law. NBIC, ASME, and/or state or local codes may apply. An AI sees to it that repairs are made properly. For example, cutting out a damaged section of tube and replacing it with a window (Fig 16) is the wrong approach; the dutchman in Fig 17 is the correct way. Likewise, the wrong and right ways to fix a leak are illustrated in Figs 18, 19.
The welding processes most often used in making boiler repairs are (1) GTAW (TIG), SMAW (stick), and a combination of both. Each has its pros and cons. For example, the benefits of TIG are cleanliness, purity, and manageable weld profile. Stick is faster. The combination offers you the best of both worlds. The negatives: TIG requires highly skilled welders and the process may be sensitive to local conditions. Stick welding requires skilled welders to get the proper results, plus proper rod selection is a critical element of the process. Rod control once the job gets rolling is critical; mixing of rod types will adversely impact weld quality. CCJ