Users push tomorrow’s automation technology into today’s plants
It’s no secret that quality technology transfer takes place increasingly at user-group meetings. The 2013 Ovation Users Group meeting, sponsored by Emerson Process Management Power & Water Solutions, was no exception. Highlights included: experience with virtualization; the expansion of open-architecture connectivity; more innovation in wireless applications; making valves smarter; escalating situational awareness for operators; and embedding advanced predictive, prognostic, and optimization capabilities in control systems.
When you consider the presentations as a whole, perhaps the greatest revelation is that the promise of a fully integrated automation and plant knowledge management platform is now being realized. The days of data streams in silos, disparate plant control systems, and narrow one-off applications is over. If your goal is to streamline data systems, it appears possible now to standardize on one enterprise platform for the entire plant.
Next new thing is here
At the end of the article summarizing key points made at the 2011 Ovation Users Group meeting, “Ovation users glimpse the future, consider today’s solutions,” CCJ editors mentioned virtualization in the section “What’s emerging.” This year, in-plant experience was reported by one user with a virtualization pilot program at a coal-fired plant. The technology is applicable to many varieties of plant computers.
Virtualization in this context refers to using software to get more productivity out of existing computer hardware. It allows you to run multiple operating systems on one physical machine by creating a “virtual machine” using software that replicates what the operating system does in the hardware. While the technique, based on technology from VMware, has been prevalent in Windows-based workstations, Emerson also has applied similar technology to Ovation controllers, valve-position modules, and Ethernet link controllers used for simulation.
The result: This coal-fired plant added several operator screens in the control room with a minimum investment in added computer infrastructure (Fig 1). Another benefit is that it is much easier to recover from upsets using software rather than rebuilding workstations. The plant is considering extending the virtualization to domain controllers, database servers, and historian, as well as adding virtual simulation.
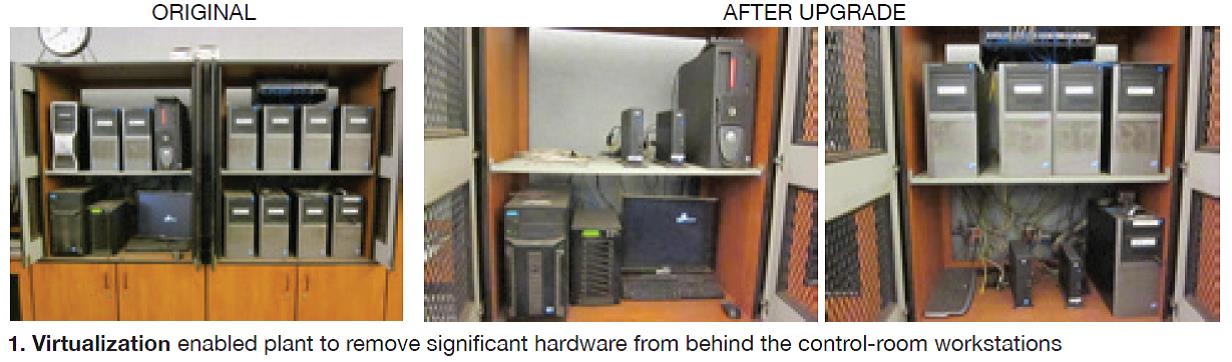
Situational awareness
One of the unintended victims of digital technology has been plant operators. The issues include data fog—too much information coming at them improperly organized—and poor human machine interfaces (HMI). Earlier this year, CCJ summarized a presentation by Harvey Ivey, manager of I&C systems and field support for Southern Company, on HMI given at the EUCI-Pearl Street Inc conference, “Managing the Digitally Integrated Power Plant.” Ivey gave a similar presentation at the Ovation meeting.
A representative from one of the largest global powerplant owner/operators offered his company’s experience on ergonomic design, incorporating control-room layout as well as operator graphics. It should be noted that both Ivey and this user referenced “The High Performance HMI Handbook,” by Bill Hollifield, a consultant specialist with PAS Inc, Houston. In this case, pictures really are worth a thousand words, when you compare the control room layout designed by the plant personnel (Fig 2) to that by the architects.
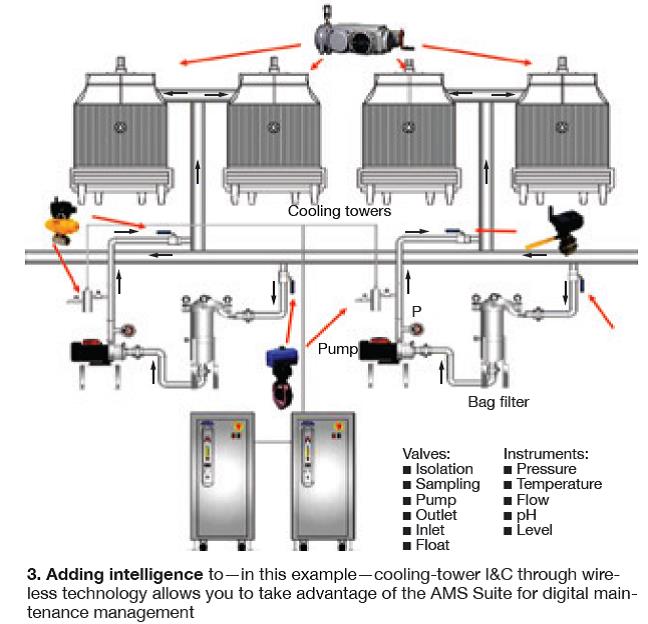
To design a control room, the owner’s task force undertook an elaborate “adjacency” analysis to determine how the main elements of the control room should be positioned relative to each other; and a sight analysis, how things should be positioned relative to the operator’s eyes. The keys to their thinking on HMI were (1) to give information to the operator about the state of the equipment, not explain to them how a powerplant works, and (2) to develop their own standards and conventions for mimic displays, relative attention and value/priority ranking, navigation, and linkage to Ovation graphics.
Gone wireless
One of the most unheralded advancements in automation is the progressive capability of wireless technology. Emerson’s Joe Cipriani and Scott Stofan made this point emphatically, declaring, “wireless applications aren’t niche, they are everywhere!” Although cybersecurity has been cited as a barrier to wireless, best-in-class solutions are available to keep wireless networks safe. The presenters noted that, for a typical boiler or HRSG 300 meters from a control room, wireless can reduce capital cost for instrumentation by 42%.
These devices are no longer for remote equipment too expensive to instrument in wired networks. As just one example, a customer purchased 117 wireless devices, 56 pressure and 61 temperature sensors, for a set of five turbine/generators at one power station. As a result, operator rounds have been sharply reduced, downtime reduced through better diagnostics, and startups are quicker because the plant can take advantage of fast-start logic enabled by the new measurements.
For one of its plants, a West Coast utility reportedly cut maintenance on the turbine compartment by 50%, improved turbine efficiency, lengthened cooling fan life, and reduced parasitic power consumption. This was through wireless temperature transmitters that indicate hot-air leaks in the turbine compartment, pressure transmitters that detect cooling-air leaks from forced-draft fans (reducing amperage), and DP transmitters that detect air-filter plugging. Other wireless technology examples cited include boiler-feed pumps, economizers, feedwater heaters, air heaters, cooling water intake facilities, generators.
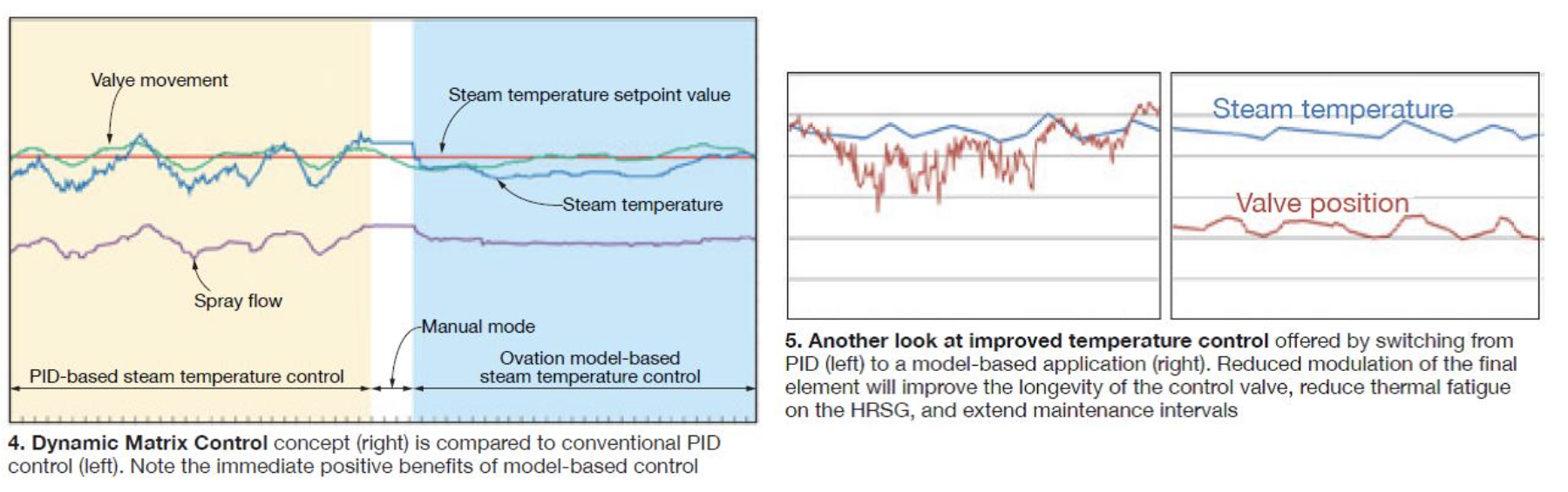
Valves—smart and ordinary
Not everything in automation involves the glitzy new digital smarts. Desuperheaters are a problem area in many combined cycles. Improper desuperheating causes tube stretching, tube metal failure, cold-reheat header cracking, water hammer, spray-nozzle failure, and other ills, noted Josh Crompton, of the Emerson Fisher Power Team. Although some plant personnel have not been informed of such, he recommends that spray nozzles in all desuperheaters be replaced every 18-30 months, and that insertion-style nozzles be inspected annually. Plus, strainers always should be used upstream of the spray-water control valves.
Severe-service valves for combined cycles include feedwater control, with the most common problem being leakage. Entrained particulates often cause erosion conducive to leakage. For this application, the severe-service valves generally recommended have protected seats and large passages to allow particulate through without inducing damage.
Of course, adding smarts to your valves shouldn’t be neglected. Mike Rooney, Emerson Process Management/Valve Automation, calls intelligence to electric actuators serving turbine isolation/main steam stop valves, boiler-feed and makeup water pump valves, boiler drain valves, cooling-tower pump discharge (Fig 3), and others “a perfect application for wireless technology.”
Adding intelligence this way allows you to open and close valves remotely; detect loss of power phase, torque switch trip condition, motor overload trip conditions, and loss of internal control voltage; check on remote enabled commands; and monitor actuator position. At the valve, you can detect jammed or stalled conditions and conditions leading to increased force to operate. In addition, all the valves can be monitored and managed through the Emerson AMS Suite using a consistent dashboard to organize all the relevant valve information in one place.
Predicting, optimizing
Predictive control is the “next generation,” according to Jeff Williams. Emerson’s version of model predictive control (MPC), a generic class of algorithms, is called Dynamic Matrix Control (DMC). Essentially, the control of the process is performed by comparing step changes in control response to a predicted response based on the model. There is a “control” horizon and a “prediction” horizon.
Models are formulated using control variables, manipulated variables, and disturbance variables. The technique essentially replaces the traditional PID (proportional integral derivative) used for decades in powerplant control (Figs 4, 5). PID is a reactive technique, DMC is a proactive technique, noted Williams. Emerson has developed models for steam temperature control, load control, and optimization.

While there are still limitations as the models are refined, two plants reportedly are running optimization models successfully. For combined-cycle plants specifically, Williams, in another presentation, covered loading optimization across multiple units, compressor wash optimization, and unit response optimization for cycling and responding to the ancillary services markets (Figs 6, 7).
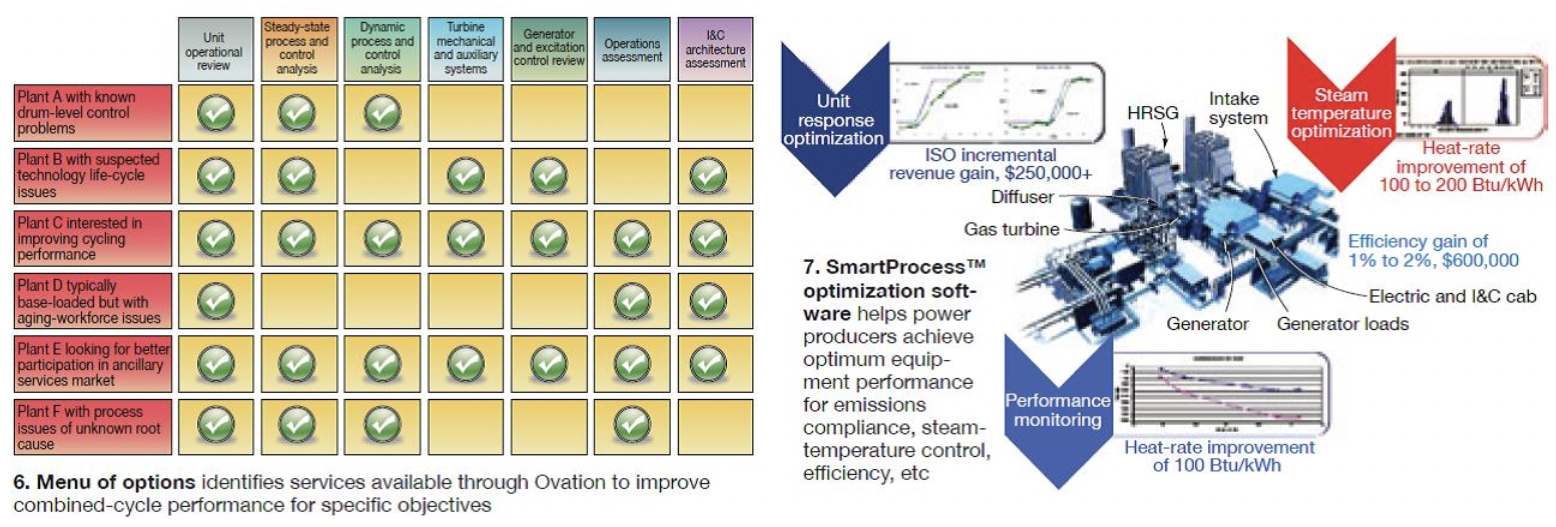
Ovation innovation: User group confers project-of-the-year awards
Part of the Ovation User Group experience these days is to honor and formally recognize colleagues who have demonstrated and/or pioneered controls innovations and successfully completed complex projects. Those recognized this year, only one a combined cycle, reflect the material discussed in the main article.
Southern Company’s Plant Hammond was selected from among entrants in the powerplant category for its Unit 4 DCS replacement. An Ovation system replaced a vintage Foxboro DCS for the boiler and selective catalytic reduction (SCR) units, and Woodward Governor controls and mechanical speed control for the boiler-feed-pump turbine drives. Goals of the project included NERC cybersecurity standards compliance, better graphical interfaces and remote monitoring of the DCS graphics and logic, updated simulator software and models, higher level of M&D on transmitters and valves, and better alarm management.
ConEdison’s 59th St station steam plant was also selected. The Ovation retrofit there was part of a larger conversion to natural gas for this vintage district heating facility. Controls for the station’s two annex boilers (550,000 lb/hr each) and three 150,000-lb/hr packaged boilers were replaced, as were the PLC-based burner management controls on the annex boilers, and common demineralizer controls—all combined into one common platform. Included also were a high-priority alarm monitor system, Ovation process historian, security manager, EDS, SmartProcess Global Performance Advisor, and tie-back simulator.
One project cited by Robert Yeager, president, Emerson Process Management Power & Water Solutions, for the strength of its nomination, but ultimately not selected, was Constellation Energy (now Exelon) Westport Unit 5 control system upgrade. This was Emerson’s first retrofit of Ovation on a Pratt & Whitney Hi-Cap system, of which only a handful are in existence. The new controls allow balancing and load sharing among the eight engines (eight gas generators, four expanders) comprising this 132-MW facility, and has improved starting and overall reliability from 50% to 100%, according to the applicants.
Other projects cited by Yeager from the pool of nominations were PENSA’s San Jacinto-Tizate Geothermal Power Plant in Nicaragua, NB Power Generation Corp’s Belledune Generating Station WDPF-to- Ovation migration, Xcel Energy’s Sherburne County coal-yard controls replacement, WE Energies’ Ovation model-based optimization at the Presque Isle Power Plant, Duke Energy’s Zimmer Station turbine controls replacement, and Basin Electric Power Co-op’s plant-wide automation at Dry Fork Generating Station.
Project-of-the-year for the water industry was King’s County South Treatment Plant for its supervisory process control. A replacement of PLCs and Forney Corp controls with Ovation was done while the plant was on-line, with no disruption to operations.
For controlling the impacts of cycling, Emerson adds capability that more precisely controls steam temperatures, controls ramping consistent with limitations of the HP steam drum, and ramps at the highest rate allowed by the steam turbine, all in a coordinated fashion. Most combined-cycle control schemes do not optimize the start-up process, because of the low level of automation provided in the original design.
When it comes to gas turbines and combined cycles, it is important to realize, or remember, that the monitoring system typically provided by the OEM is for protection only, to guard against a catastrophic failure. That is, they shut down the unit if any out-of-bounds conditions are detected. Reuben Wunder, a subject matter expert for Emerson’s Machinery Health Management business, discussed how Ovation users can go beyond the traditional protection measurements, including turbine bearing accelerometers, turbine axial thrust, turbine case vibration, intake pressure, intake pressure, speed, and shaft position.
Today, Ovation products include a complete turbine monitoring solution fulfilling API 670 criteria for key monitored areas, as well as predictive monitoring that goes well beyond protection. Backbone of the solution is the CSI 6500 prediction system which includes eddy- current probe resting and dynamic position, full-spectrum analysis to detect turbine/case rubbing, and interactive 3D displays of the turbine shafts. Also featured:
- Simultaneous and continuous transient recording of all protection channels at over 5000 samples/ second.
- Patented PeakVue technology to monitor turbine bearings.
- Ease of integration with CSI data populating Ovation faceplates.
But Ovation can also “layer on” to the existing protection and supervisory systems. Wunder illustrated this using an Ovation retrofit at a powerplant that converted to combined cycle from a simple-cycle unit. This was said to be one of the first Mark VI controls retrofits. In this case, Emerson integrated the GE EX2100 excitation system such that its functionality can be controlled through Ovation, and included the AMS Suite, and the CSI6500. In subsequent phases of the project, Ovation will provide direct control and monitoring of the HRSG, burner management system, feedwater and water treatment systems, substation equipment, and steam-turbine supervisory control.
In another example, during commissioning of an 8100-rpm, 1500-hp turbo-compressor, a high vibration level was detected in the expander, but because no mechanical issues were discovered, the vibration alarm levels were raised and the turbine operated for a year. To determine the root cause, the plant brought in Emerson to overlay its prediction system onto the protection system. Immediately, noted Wunder, the system revealed a sub-synchronous vibration component and the sub-synchronous peaks were creating an unstable orbit.
Well-connected automation
The example above is only one illustration of how Emerson has positioned Ovation as a platform, the gateway to other plant knowledge systems, as well as a completely integrated automation and enterprise solution. The table shows how well connected Ovation is to third-party systems important to combined-cycle owner/operators.
Emerson has completed over 600 retrofits for gas-turbine control systems, and continues to acquire new references on legacy automation systems provided by OEMs. Emerson’s Laurence O’Toole and David Cicconi, in their presentation, listed the following models for which Emerson has retrofit experience: Westinghouse 171, 191, 251, 501 (all models); GE Frames 3, 5, 6, 7 (all models); Siemens 84.2, 64.3; Pratt & Whitney FT4, GG3, GG4; GE aeros LM2500, LM1600; Alstom GT9, GT11D, GT11N; and various models of Solar, Rolls Royce, and Ruston gas turbines.
Next up is the LM6000. Emerson has invested in a two-year development program around the automation of this engine and is in the commissioning stages for its beta commercial project, four LM6000s for a facility in the Midwest. To overcome a key challenge with such retrofits, embodied by the question, “How am I supported when I go away from the OEM?” Emerson has developed alliances with PSM/ Alstom and Mitsubishi Power Systems Americas to provide a complementary suite of support services.
In a similar vein, Thor Honda, business development manager for steam turbine controls, discussed the many Emerson retrofits of steam turbine controls for ABB (ProControl, Advant, Turbotrol), Toshiba (TOSMAP-DS), Alstom (P320,P400), and GE (Mark V and VI), providing multiple examples in each category. Most of these legacy systems are no longer supported, not supported well, or were troublesome for plant owner/operators in the first place. Honda also addressed Emerson’s rotor stress solutions, which allows for shorter startup and loading sequences than typical OEMs’ loading curves. One of Honda’s eye-opening graphics reveals the difference in technology evolution of a steam turbine and automation system elements (Fig 8).
Ovation connectivity platforms | |||
Serial link controller | Ethernet link controller | SCADA | Third-party 1/O |
Protocols (Ovation release independent) |
Protocols (Ovation release independent) |
Protocols (Ovation release dependent) |
Protocols (Ovation release dependent) |
Allen Bradley GE Mark IV IEC 870-5-101 Ingersoll-Rand MP3 Modbus master Modbus slave Vilter data link . . . And more Time stamping Graphic application |
Allen Bradley CSP client Allen Bradley DF1 client Allen Bradley EIP client (native and PCCC) DNP 3.0 client DNP 3.0 server GSM 1 and 3 client IEC 60870-5-101 controlled IEC 60870-5-101 controlling IEC 60870-5-104 controlled IEC 60870-5-104 controlling IEC 61850 MMS client Modbus master Modbus slave OPC tunnel . . . And growing Time stamping Graphic application |
Allen Bradley EIP client (native and PCCC) Bristal Open BSI 5.8 DNP 3.0 client DNP 3.0 server Modbus master Modbus slave WestGate master . . .And growing Time stamping Graphic application |
Allen Bradley External Ovation network GE Genius GE Mark V/VI/VIe MHI Modbus master RTP IO Toshiba Wireless HART OVATION SIS Scan type Time stamping Graphic application |
It bears noting that the enhanced monitoring, diagnostics, and prognostics go hand in hand with the ability of independent service providers to support a facility at equivalent or higher quality for less money than the OEM. Much of the domain expertise and diagnostic work that would have been performed by OEM technicians, often at exorbitant labor rates, or by the OEM’s remote monitoring facility, can now be done through advanced diagnostics.
It often is said that the information about the hardware is becoming more valuable than the hardware. For many of the gas turbine and CC plants which came on-line in the late 1990s/early 2000s, the control systems are reaching the end of their lives, or are becoming obsolete and not well-supported by the OEM. This is not only an opportunity to replace a control system, but to lock in aftermarket services around the hardware as well and provide a standardized platform for owner/operator organizations (Fig 9). In a big data driven world, he who controls the data wins. CCJ