An A Comprehensive Approach to 7A6 Generator Life Cycle Management
Presenter
Russell Chetwynd, Service Manager
Mr. Chetwynd has been in the Power Generation business for over 40 years. He started out as a student apprentice for GEC Turbine Generators (now part of GE) in the UK, going on to work as a Commissioning Engineer starting up fossil and nuclear plants around the world. He then spent a large part of his career with Southern California Edison as the Site Engineer responsible for turbine generators at the San Onofre Nuclear Generating Station (SONGS) in northern San Diego County, CA USA. While in this capacity, Russell became heavily involved in industry activities, authoring numerous technical papers and serving as Chairman for both the Electric Power Research Institute (EPRI TGUG) and the American Society of Mechanical Engineers (ASME) turbine generator committees. Upon closure of SONGS in 2013, Russell joined National Electric Coil as a Service Manager responsible for large utility accounts in North America and Australasia.
Presentation Synopsis
Industry experience has revealed a litany of concerns with the 7A6 generators that are typically married to the 7EA gas turbine. These include: stator failures traced to housing leaks, stator-winding partial discharge, rotor main lead failure, stator end-winding looseness (dusting and greasing), rotor-turn insulation migration and rotor copper elongation and foreshortening. Many of the rotor issues stem from the 7A6 generator rotor not being designed for the extensive cyclic operation now being experienced to accommodate additional renewable generation on the grid. The rotational forces, or cyclic loading, results in fatigue of rotor components not designed for this type of operation. This presentation will discuss these life cycle management issues in more detail and outline the solutions that have been successfully implemented, by the author’s company and are now readily available.
Key Takeaways for Users
Whether owner has a fleet of 7A6s or just one, this presentation will be useful to asset managers, maintenance planners and plant engineers, alike. These life cycle management issues can have impacts on budgets and outage planning and execution. Awareness of specific issues and the related failure modes can enhance and improve both preventive maintenance activities and long-term outage planning.
Contacts
Steve Jeney, VP Sales and Marketing, 614-580-9306, sjeney@national-electric-coil.com
Howard Moudy, Director of Operations, 724-787-4967, hmoudy@national-electric-coil.com
Russell Chetwynd, Service Manager, 949-939-3307, rchetwynd@national-electric-coil.com
Eddie Yates, Service Manager, 225-588-5322, eyates@national-electric-coil.com
About National Electric Coil
NEC provides the "Total Generator Solution" for high-voltage generators of all makes and sizes, manufacturing a wide range of types of windings for stators, rotors, fields and exciters. NEC also has a full-service engineering staff available for failure analyses, testing, uprates and replacement component design, including engineered solutions for all OEM service bulleting issues. With a fully-equipped facility with balance pit and on-site field services, NEC ready to address the needs of any generator maintenance, repair and overhaul (MRO) project. ISO9001-certified QA systems.
Products and Services
- New and replacement winding manufacture for generators
- Rewind, overhaul and retrofit services
Website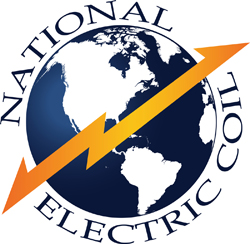
www.national-electric-coil.com
Address
800 King Avenue
Columbus, Ohio 43212
United States