Challenge. In preparation for the OSHA Voluntary Protection Program (VPP) review, the facility needed to better address ergonomics as part of their job hazard analysis (JHA). Ergonomics is an often overlooked hazard in the workplace.
The definition of ergonomics is basically the study of work and how it is to be done properly. It is the science of how human body works and the equipment design that maximizes productivity so people can be utilized to their highest potential. In other words, it is the study of how things are done in the workplace and the measures to be taken so a worker can be comfortable and at the same time be able to produce at the highest level.
Solution. The success of this program starts with training personnel to perform hazard assessments, empowering them to identify and correct deficiencies, clearly explaining the purpose of policies, and not just stating them for employees to memorize and follow. Keeping with this philosophy we formed a small team to devise an ergonomic program that followed the method of our safety culture. The original concern was that ergonomics would focus only on the best way to sit in a chair or hold a mouse.
An occupational therapist provided ergonomics training and workplace assessments. The trained nurse walked around the facility with the ergonomic program team and evaluated routine tasks employees performed.
Discussions were held on proper posture while at a computer, proper table height, working on concrete floors, heavy lifting, and repetitive tasks (Figs 1, 2). Non-routine tasks—such as crawling in HRSGs to perform inspections and repairs, working in turbine compartments, and elevated work during outages—are contributors to ergonomic injuries at industrial sites.
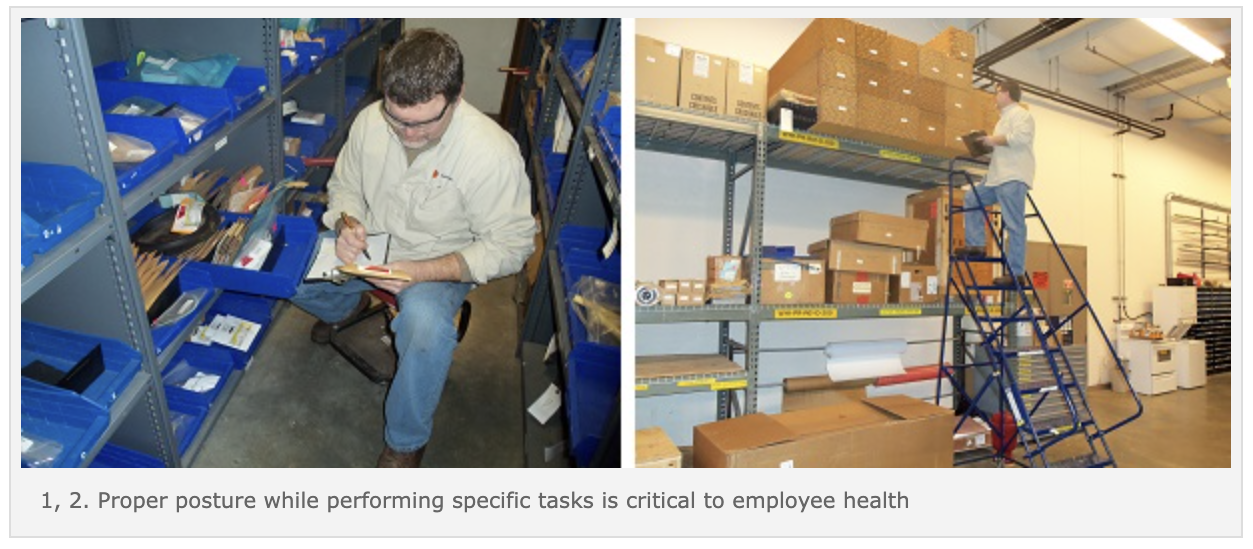
The team found other informational items from safety companies that provided guidance on ergonomic programs in industrial facilities. Members of the safety committee also attended VPPA conferences and conferences on ergonomics, which were particularly helpful in the design of our program.
Results. The facility was able to implement a plan that incorporated ergonomics into our everyday safety culture. An ergonomics plan was established which provided guidelines for routine and non-routine work that exposed employees to ergonomic hazards by adding ergonomics JHA, an ergonomic review on our work permits, and a method for employees to recommend improvements to the safety committee.
An ergonomics review is conducted quarterly by the safety committee and the plant controller. The occupational therapist provides training to all employees and is now incorporated into our annual training plan. Our ergonomics program helps provide protection from ergonomic injuries and is incorporated into our overall safety culture.
Key project participant:
Sam Graham, maintenance manager