At the upcoming virtual 501F Users Group conference, owner/operators will have the opportunity to hear the latest on solutions for leaky 4-way joints. Below is a primer and brief history of Nord-Lock’s experience in mitigating this common problem in the fleet. The latest information on their solution will be presented on Tuesday, February 23 from 2:10-2:40pm EST during one of the the 501FUG’s Vendorama sessions. View the full agenda and register here.
The editors can’t remember a meeting for Siemens 501F users that didn’t include at least a mention of leakage at the 4-way joint. A typical fleet-wide remedy was to weld on so-called leak boxes to prevent leakage from offending joints (Fig 1). These, of course, had to be removed during an outage and then reinstalled before resuming operation.
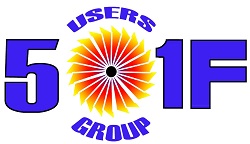
Nord-Lock Group VP Peter Miranda discussed his company’s engineered approach to preventing leakage at the 4-way joint in a Vendorama session at the 2020 501F Users Group meeting at the Hilton West Palm Beach, February 10, a month prior to the onset of Covid-19 restrictions. Nord-Lock has continued perfecting its solution since and a progress report on that work follows.
Miranda’s presentation can be reviewed by registered 501F owner/operators on the user group’s website. Non-members who meet the organization’s requirements can gain membership status by completing the online registration form.
Background. New turbine cylinders are perfectly aligned, faces flush, with no leaks at the joints. Over time, extreme thermal variations and startups lead to warping and distortion. Cylinder misalignments compound the problem because flange surfaces must maintain the maximum contact area needed to ensure a proper seal, allowing leaks to occur.
Another contributor to leakage is the lack of an upper-half spigot, which is removed after final assembly in most cylinders. The concept here is simple: Emulate the lower-half spigot (Fig 2) on the upper half since pressure inside the combustion chamber will affect these exposed areas and cause leakage through cylinder joints, bolts, or bolt holes.
The helicoil bolt-hole misalignment shown in Fig 3 is evidence of cylinder displacement of the flange face. To remedy leaks, the misalignment must be addressed. If holes can be forced into alignment and maintain concentricity during loading, the flanges likely will sit flush, preventing the leak. Proper tension of the joint is critical to success.
Leaks can cause significant damage to instrumentation and insulation, and also jeopardize operations and worker safety. Maintenance is required to weld-on leak boxes (refer back to Fig 1) to contain the leak and requires removal and reinstallation during an outage—adding time, resources, and cost to the outage schedule.
Update. Nord-Lock Group partnered with a Siemens 501F user on an R&D project to investigate 4-way-joint leak issues with the goal of finding a fleet-wide solution. The partners consider remedying leakage issues important for the protection of both personnel and critical equipment. A comprehensive testing program was identified, then validated on several units, as an effective solution—one that combined multiple Nord-Lock products and technologies.
Solution. Given the multiple contributing causes of 4-way joint leakage, the most effective solution identified combines a specific mix of products and technologies. The combination works in concert to address multiple potential failures and provides the following advantages:
-
- To quickly assess and manipulate cylinder alignment, the solution includes a Boltight™ hydraulic closure system (HCS, Fig 4). This ensures the 4-way joint is tensioned, temporarily, to conduct a proper alignment check of the cylinder—one similar to the tops-on/tops-off alignment checks performed on steam turbines.
- If the bolt hole or flange is misaligned, a proprietary CamAlign tensioner system is used to realign the cylinder. The system can close an internal gap of the cylinder by 10 to 15 mils after the cylinder has been “squeezed” by the HCS, to ensure the smallest possible gap is achieved.
- The HCS is pressured up to simultaneously and uniformly squeeze the turbine cylinder around the 4-way joint—thereby isolating the area. Multiple hydraulic tensioners remain pressured up while internal and external gap readings are recorded, and cylinder alignment is checked.
- Once adjustments are complete and the 4-way joint is aligned properly, the joint is squeezed again using the HCS, which allows load transfer to the Superbolt™ mechanical multi-jackbolt tensioners—to permanently tension the joint—without losing tension on the joint.
- Rather than tensioning one bolt at a time, which can continually create movement of the load, the HCS immobilizes the entire joint.
- An internal seal is installed to reduce leakage at the 4-way joint area where the cylinders for the combustion and turbine sections meet (Fig 5). The seal functions to eliminate any leakage paths that cannot be corrected by realigning the cylinders.
- Aggressive operating requirements and maintenance schedules needed to keep pace with operating requirements contribute to misalignments that cannot be corrected completely with CamAlign. The seal provides an added layer of leak protection.
Over the course of several installations, variations were noted in spigot fit and seal shapes. Internal seal retainers were redesigned to allow for thermal growth and variations in the cylinders.