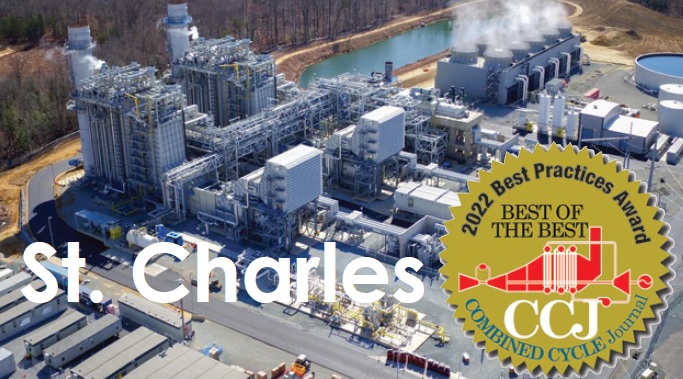
St. Charles Energy Center (SCEC) was commissioned in February 2017. Near the end of 2019, the plant experienced a through-wall leak at a girth weld on a hot-reheat (HRH) bypass line to the condenser, resulting in forced-outage time and the loss of generation revenue. But most concerning was that this was a significant safety concern which could result in a catastrophic failure.
Plant management reached out to Structural Integrity Associates Inc to aid in the analysis of the weld failure. A ring section containing the failed girth weld was removed and submitted to SI’s materials lab for review. Thermal fatigue was determined to be the most likely cause of the failure.
Staff worked with Structural Integrity to install local thermocouples (t/cs) around the failed area of the HRH bypass to assess the magnitude of thermal transients experienced during load-change events and normal operation. In sum, four t/cs were installed on the top, bottom, and sides of the pipe along with a local data logger. Over 30 days that the data logger was in place, temperature variations of up to 700 deg F were observed around the pipe circumference during load-change events.
The live data collected by the t/cs and data logger were analyzed by SI and sent to the manufacturer of the bypass valve. The supplier used these data to redesign the HRH bypass-attemperator spray-nozzle assembly while plant staff modified the attemperator’s logic to reduce the large temperature swings and the piping thermal stress they created.
Failure of the HRH piping weld worried staff because the facility had been operating for only two years. Staff was concerned there may be other unknown high-energy-piping (HEP) issues in the plant that could lead to a failure prior to a regularly scheduled inspection.
These concerns were expressed to Structural Integrity, which proposed a wireless sensor network and t/cs to remotely read data in near-real-time and incorporate the t/c readings into St. Charles’ PlantTrack online database.
SI’s first step in making a timely transition from the facility’s traditional HEP asset-management roadmap to “smart data” monitoring was a risk assessment. The methodology used is known as Vindex™ (for vulnerability index). It considers factors such as creep life, Grade 91 risk factors, failure consequences, etc (Fig 1).
This approach incorporates inspection history and key component characteristics using structured and consistent methodologies that can be used across several piping systems. Each weld, or location of interest, was assessed according to component damage potential and consequence of failure.
The Vindex provided risk scores for each weld and for each pertinent system within SCEC’s PlantTrack database. Risk scores determined the HEP locations that would benefit from active online monitoring. The engineering study concluded t/cs should be installed at 10 locations (Fig 2) and active online pipe-hanger position monitors at nine. The latter provide real-time hanger-position data to the PlantTrack system to better understand and predict high-stress locations within the piping system.
The wireless sensor network consists of two primary components: (1) sensor nodes that collect local sensor data and transmit it wirelessly to (2) a gateway that transfers the data to the PlantTrack database. Fig 3 illustrates SI’s data collection node, highlighting several of its features. Each node has multiple sensor channels and is capable of collecting data from a variety of sensor types. The single node can accommodate up to nine different standard t/cs.
The wireless data-acquisition node is installed in close proximity to the monitored component, and all thermocouples are hardwired to the node. Data from all nodes are transmitted via a 900-MHz wireless protocol to a locally installed Wi-Fi-enabled gateway, which stores the data in a local database until they are transmitted successfully to the PlantTrack cloud database. Once transmitted offsite, data can be accessed through SI’s PlantTrack web interface. Fig 4 summarizes the general wireless sensor network infrastructure implemented at SCEC.
This project has resulted in a highly valuable tool for targeting inspections and planning outage scopes more efficiently. The active tracking of temperature differentials with strategically placed t/cs provides a means to quantify the number and accumulation of thermal-transient events within individual sections of the HEP network.
Inspections are planned and performed based on live data and detected damage rather than calendar time. This amounts to a huge cost saving for the facility. Without this system in place, an event like the HRH failure in 2019 would have required annual piping inspections to ensure a problem is not developing again, but with the active t/c data staff is able to monitor piping in real time to determine if and when an inspection is necessary.
In addition to gathering real-time data, the monitoring system has been configured to send email alerts when events of certain magnitude occur, or based on trends-in-temperature events. SCEC personnel are notified immediately when temperatures climb above set limits and when impingements occur. Quarterly calls are held with subject matter experts from Structural Integrity to review the data and discuss any areas of concern or further operational improvement. PlantTrack Online is also connected to the site data historian, which uses additional sensor data to aid in diagnosing and trending attemperator damage.
In sum, by implementing the wireless HEP monitoring system, SCEC has proactively improved plant safety and reliability, while reducing O&M costs and the potential for losing generation revenue. By routing the data to an online database with integrated analytical algorithms that transform data into operational intelligence, St. Charles is able to make timely and informed decisions about plant operation that will maximize the life of critical components and ensure personnel safety.
Plant personnel at the forefront of this project were Jonathan Bennett, Jacob Boyd, and Nick Bohl.