The Air-Cooled Condenser Users Group (ACCUG), established by NV Energy in 2009, has recently publish technical guidance document ACC.02, Guidelines for Finned Tube Cleaning in Air-Cooled Condensers. This document includes fundamental principles, operational factors that can limit efficiency, types of tube fouling, debris removal methods and examples, cleaning frequency, as well as safety and environmental concerns. Following is a overview.
Heat transfer surface and fans. Air-cooled condensers use specialized heat-transfer tubing; the current tube design most commonly employed is aluminum-clad carbon steel tubes with exterior aluminum fins (to increase air-side surface area). Tubes are normally oval or rectangular with approximately 0.059 in. wall thickness and closely-spaced fins (Fig 1). Over time, these fins become fouled with debris.
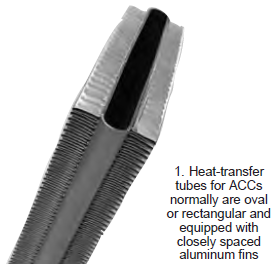
In most cases, air flow around the tubes is provided by large fans positioned below the tube bundles, directing cooling air upward in a forced-draft configuration.
During plant operation, steam from the low-pressure steam turbine is directed via large ducts to the top of the heat exchange tubes. Moving down the approximate 36 ft tube length, steam is condensed to liquid water by releasing the latent heat of vaporization, and the water returns (as condensate) to the steam generation process.
Because air is a relatively inefficient heat-transfer medium, ACCs are large elevated structures with considerable surface area. Efficient optimization in both design and operation are critical to viable plant operation.
Operational factors limiting efficiency. Inefficient ACC operation can result in higher system backpressure, less efficient plant operation, and possible turbine trips. As efficiency declines, more steam (and fuel) is required to maintain megawatt output.
The cooling fans moving high volumes of air through the narrowly-spaced fins will inevitably result in the accumulation of airborne debris on the fan side of the tubes. Blockage of air passageways prevents optimal heat transfer, reducing steam condensing efficiency. Debris is often site-specific, and may include vegetation (cottonwood seeds, leaves), trash, animal sources (birds or bats, feathers, flying insects), and local sources such as industrial byproducts (cement factory or coal dust, etc). One common and particularly troublesome foulant is oil from fan gearboxes.
Ambient temperature is a major factor in ACC operation, and any detail that improves heat transfer, such as maintaining clean tubes, should be optimized.
Cleaning/removal. The most common foulant removal method is pressurized water, applied from the exterior (top side) of the unit. This is typically performed by a semi-automatic system that moves multiple spray nozzles vertically on a track that can also be manually moved in the horizontal direction (Fig 2). Water quality and direction of spray are important to avoid fin damage and risk of tube corrosion.
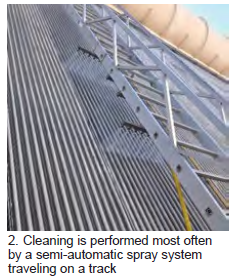
Cleaning system and medium options are discussed in the document.
Frequency. The need for cleaning should be evident by observing deterioration in condenser performance as described in the document. Visual inspections are also important.
It is common for operators to report significant improvement in overall plant performance following cleaning. Finned tubes typically require cleaning once per year, but site conditions may require more- or less-frequent action. Ambient temperature and humidity factors are also important and are discussed.
Implementation. Full implementation details are reviewed including safety and environmental concerns. Factors include equipment and water supply, personnel requirements, site planning, and the effect on other equipment and systems during cleaning (neighboring fans, water protection for electrical equipment, etc). Seasonal, temperature, and safety recommendations are included.
Other ACCUG reports. This document is in final review and will be issued early 2019, and available on the website. Guidance document ACC.01, Guidelines for Internal Inspection of Air-Cooled Condensers, was issued in May 2015 and is available at no cost to users.
ACCUG’s charter is to foster collaboration among owner/operators of powerplants with air-cooled condensers, enabling chemists, engineers, and O&M personnel to grow professionally and maintain their plants at peak performance while reducing expenses. Group participants include water chemists and operational personnel at steam plants, combined-cycle facilities, and other types of generating stations that rely on dry cooling technology.