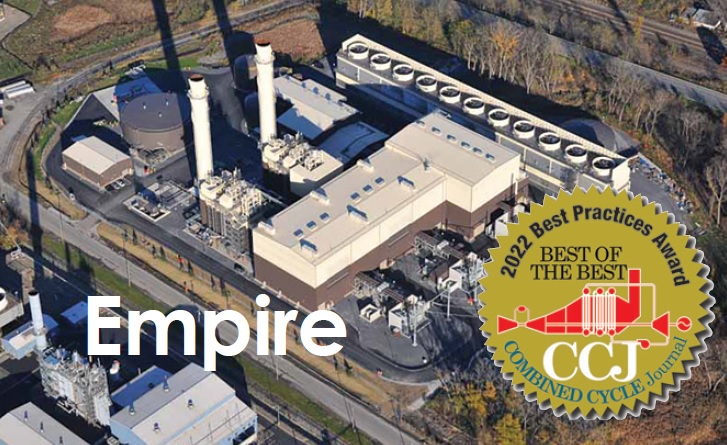
Falls are among the most common causes of serious work-related injuries and deaths. OSHA general industry standards require fall protection for persons working at heights of 4 ft or greater above a lower level (6 ft for construction). In 2021, falls remained the top OSHA citation for the 11th consecutive year.
Fall protection systems include employee equipment for fall arrest, such as harnesses and lanyards; special job-related equipment, such as travel restraints, D-bolts to attach to, anchor straps, etc; and fixed systems, such as ladders, guardrails, and gates.
At Empire Generating, individually assigned fall-arrest equipment was reaching its end of life. Plus, fixed fall-protection systems were from original construction in 2009 and some were deteriorating, difficult to use, or outdated. A thorough review was needed to identify (1) equipment which required replacement, (2) potential issues or deficiencies, and (3) better solutions to ensure employee safety and regulatory compliance.
A multi-year project began with a review to identify work tasks at heights, fall hazards, and the current systems in place. This was done by a third party, Safety Compliance Services, which produced a Fall Hazard Survey report.
It assessed all existing fall-protection equipment and systems, and fixed ladders, identifying deficiencies and equipment which should be replaced or removed, while making recommendations for upgrades. Each location or task requiring fall protection was ranked for exposure risk to assist in prioritizing projects. In addition, a plan for each location was made with recommended fall-hazard mitigation.
For individually assigned fall-arrest systems and associated equipment, a review was done based on fall hazards identified in the Fall Hazard Survey. Updated equipment was recommended—such as replacing the existing conventional lanyards with self-retracting ones (SRL), travel-restraint equipment, and the addition of other equipment. New harnesses and SRLs then were purchased and assigned to individuals.
Other equipment was set up in the turbine hall in a labeled cabinet for use as needed. All employees were fitted to their new assigned equipment and training was given by Safety Compliance Services on all of the new equipment.
Some of the items identified in the Fall Hazard Survey were done in-house—such as eliminating storage areas over several areas that would require fall-protection systems, installing several swing gates at the lube-oil and chemical bulk storage unloading area, and installing removable guardrails (photos).
L G White Safety Corp was brought in to review the plant’s fixed ladders and the other fall-protection system recommendations in the Fall Hazard Survey. A detailed proposal with photographs and recommendations was developed for ladder safety systems, rooftop equipment access, areas where rails had to be removed to bring up equipment or parts leaving edges unguarded, and where work was being done more than 15 ft from an edge.
In 2021, fall-protection systems were installed by L G White included these:
- Replacing six existing ladders on tanks and the stack ladders with 3M’s DBI-SALA® Lad-Saf™ systems that have a center tie off for fall protection and tie off points at the top and swing gates.
- Removing existing deteriorated horizontal lifelines and installing grated paths, guardrails, and self-closing swing gates for access to the roofs of the administration and water-treatment buildings.
- Installing a removable guardrail system for a turbine roof deck.
- Installing roof guardrails, swing gate, and a fixed ladder for an inside storage area over an office area (after ensuring load ratings were appropriate).
- Installation of a mezzanine safety gate in the turbine hall.
- A guardrail system to access rooftop vents that are more than 15 ft from a roof edge in several locations.
- Installation of a fixed ladder, swing gate, and working platform with rails to ensure safe access to valves on the top of carbon dioxide tanks.
Additional updates to the initial fall survey plans and procedures and training on the new systems are planned for 2022 now that those systems are in place. Annual inspections also were updated.
Plant participants in the project included Chet Szymanski, plant manager; Janis Fallon, EHS manager; Jason Glassbrenner, safety committee chair; and maintenance technicians Eric Palmer and Jim Smith. Third-party notables include Don Bessette of Safety Compliance Services and Mat White of L G White Safety Corp.