At European Technology Development Ltd’s International Conference on Power Plant Operation and Flexibility, held in London in July 2018, ETD’s Dr Ahmed Shibli, the conference organizer, and David Robertson tag-teamed an in-depth presentation on life-prediction concerns for aberrant P91 components often found in electric generating stations worldwide. They are usually the product of not understanding the precise heat-treatment requirements, by the component producers and fabricators, for high-Cr martensitic steels.
The duo issued a stark warning: “Traditional NDE techniques do not show damage in P91/P92 until late in life (70% or later), making current detection and component integrity management difficult.” New techniques are needed.
“A problem with 9Cr martensitic steels,” they said, “is that the creep cavity size for the first 70% of life can be on the nanometer or few-microns level only. Thus, cavity detection and quantification by traditional means, such as replication or UT inspection, can be difficult.”
At the same time, “for aberrant microstructures, powerplants often assume the safe life is equal to P22 or P91. But the industry could be underestimating life, thus condemning these components too early and thereby losing revenue. We currently do not have long-term rupture strength data for such abnormal microstructures to predict their safe operating life accurately.”
The two presenters gave examples of potentially abnormal materials:
-
- Material over-tempered or tempered high in the ASME range.
- Material under-tempered at the bottom of the new ASME range (730C) or old range (704C).
- Cooling too slowly from austenitizing.
- Soft spots and soft bands found in some piping materials.
Welding issues include:
-
- Various repairs and weld-repair configurations/geometries.
- Repeat weld repairs.
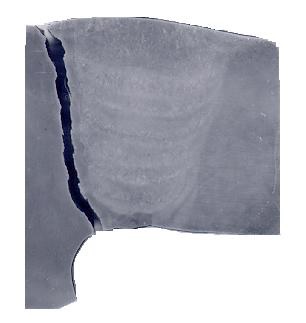
Next, Shibli outlined a six-year joint industry project that began in 2014 “aimed at producing 15 aberrant microstructures in P91 (both base and weld metals) and conducting stress rupture tests to 30,000 hours, which can then be extrapolated to 100,000 hours and beyond to estimate the safe operating life.”
Initial industry sponsors, coordinated by ETD, are various European and Japanese utilities, although new partners/sponsors are welcome at any stage to contribute towards the testing of one more of these aberrant microstructures. This project also involves detailed metallography, including use of transmission electron microscopes (TEM), to categorize the microstructures and their behaviors.
“To make matters worse and life assessment more difficult,” Shibli continued, “it is now fairly well established that the creep failure stages for high-Cr martensitic steels (P91/P92) are reduced to creep cavity initiation, cavity growth, and failure with little warning.”
Specific visual examples were given for all points made in the presentation. Featured in the examples was Type IV damage in seam-welded components (photo).
“The 9Cr martensitic steels have been very useful in raising powerplant temperatures and pressures (and making HRSGs more compact), improving plant output and efficiency,” Shibli stated. “However, more and more of these components are now showing cracking at the Type IV position associated with the weldments.”
And their conclusion: “Even components that can be identified to be at risk are creating issues for the plant owners and integrity assessors in view of the unknown long-term rupture strength of the aberrant steels, hence the need for the long-term stress rupture data to ensure their safe operation.”