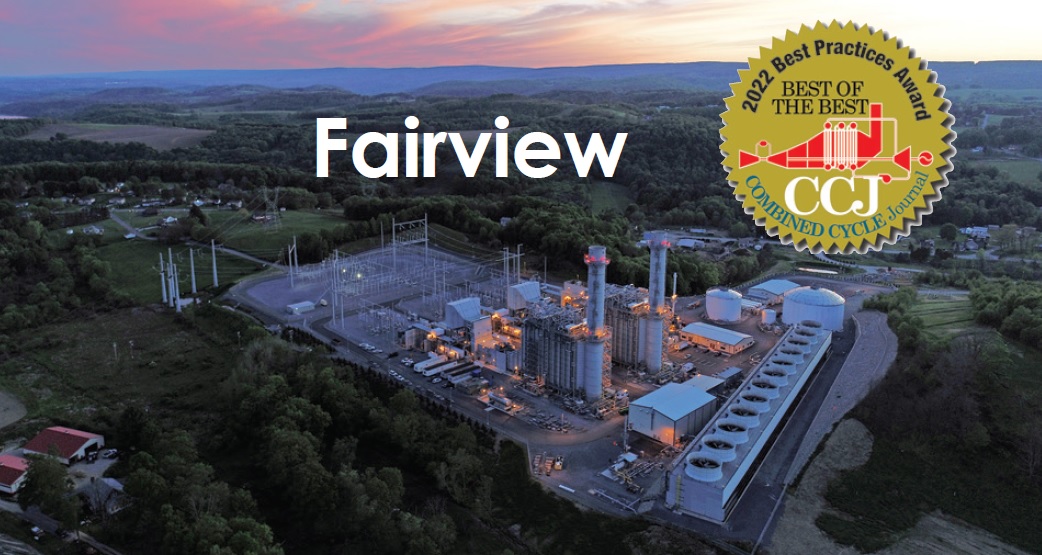
Soon after commissioning, staff discovered that a single point of failure of the ammonia-injection control valve could create an emissions exceedance, limiting the plant’s response and output, as dictated by state environmental permitting.
An hourly NOx exceedance was experienced less than one month after commissioning because of a faulty flowmeter indication. It limited the amount of ammonia injected necessary to meet the NOx removal rate at the desired load.
An alternative method for injecting ammonia was needed to maintain emissions compliance and remain online and dispatchable while operating with a fault ammonia control valve or associated instrument.
A redundant ammonia injection train was not desirable because of the time involved for procuring and installing the additional controls, combined with space challenges (Fig 6). An alternative means of ammonia injection was proposed by one of the plant’s operators—a manual bypass valve. It could be installed quickly and, if necessary, be replaced later by a fully automated redundant header with automatic control and block valve.
It was apparent that a manual bypass valve around the automated control valve would be essential for providing an alternative means of ammonia injection to prevent a NOx exceedance in cases of faulty instrumentation or failed control valve. By ensuring continuous operation with emissions limits, the plant would be able to stay online and ensure the reliability of the Bulk Electric System.
A management-of-change plan was initiated and a new ammonia line was specced out along with the valves necessary to both allow continued ammonia injection and permit safe changeout of the existing ammonia control valve in case it fails.
Success! A manual bypass control valve was installed and preset to a flow volume correlating to the ammonia injection rate necessary at baseload. The new valve reduces the probability of an exceedance by allowing expedited restoration of ammonia flow in the case of a valve or instrument fault.
As an added safety precaution for staff operating the bypass valve, a shield was installed to minimize the possibility of an operator being sprayed with ammonia accidentally in the unlikely event of a valve leak.
Site training was held on the newly installed valve and the operations required for its use, if necessary. In addition to installing the manual bypass, logic changes were implemented to make the existing automatic valves less susceptible to closing because of failed instruments. To date, the plant has not had to run with the manual bypass valve open. Presently, there is no need to replicate the automatic control and block-valve arrangement.
Employees contributing to project success included CROs Tim Krumenacker and Curtis Speer; Jason Havash, I&E technician; Jeff Lellock, engineering; and Brian Kline, O&M technician.