CCJ ONsite’s coverage of 2018 award-winning best practices from 7F owner/operators concludes here. The five entries from four plants (Bastrop, MEAG Wansley, Nuevo Pemex, and Rathdrum), all operated by NAES Corp, were recognized for their value by judges with deep knowledge of this frame. In sum, fourteen 7F plants shared 26 best practices with their industry colleagues in 2018. All of this experience is at your fingertips on the CCJ website, most only two mouse clicks away. Submissions to the 2019 CCJ Best Practices Awards will be accepted until February 15, 2019.
Installing a jockey pump yields substantial potable-water saving
Bastrop Energy Center, Cedar Creek, Tex, owned by Blackstone Energy Partners and operated by NAES Corp, was designed to receive potable water from the local utility for both domestic use and demin makeup. The system includes redundant potable-water booster pumps sized to provide adequate supply for the demineralizer.
The concern was that each pump requires a minimum flow rate of 27 gpm, and while the demineralizer is required to be in service only a few hours per day, a booster pump must remain in service 24/7 to provide adequate pressure for the restrooms, kitchen, eyewash stations, etc.
With average potable water usage well below the minimum flow rate, approximately 27 gpm of potable water was passed through a minimum flow valve and discharged to the cooling-tower makeup supply. From a water conservation perspective, this appeared to be a good initial system design; however, with the cost of potable water at $4.50/1000 gal, and the cost of river water used for cooling tower makeup at $0.50/1000 gal, an annual differential cost of approximately $52,000 was being incurred by using potable water for tower makeup.
To resolve the issue, Plant Manager Jerome Svatek and his team installed a small “jockey” pump in parallel with the two existing booster pumps, along with a pneumatic pressure tank (photos). This pump has its own local pressure switch, which cycles the jockey pump on and off to maintain adequate potable water pressure when the demineralizer is out of service and potable water requirements are small. This is similar to the type of system a homeowner would have with a private well.
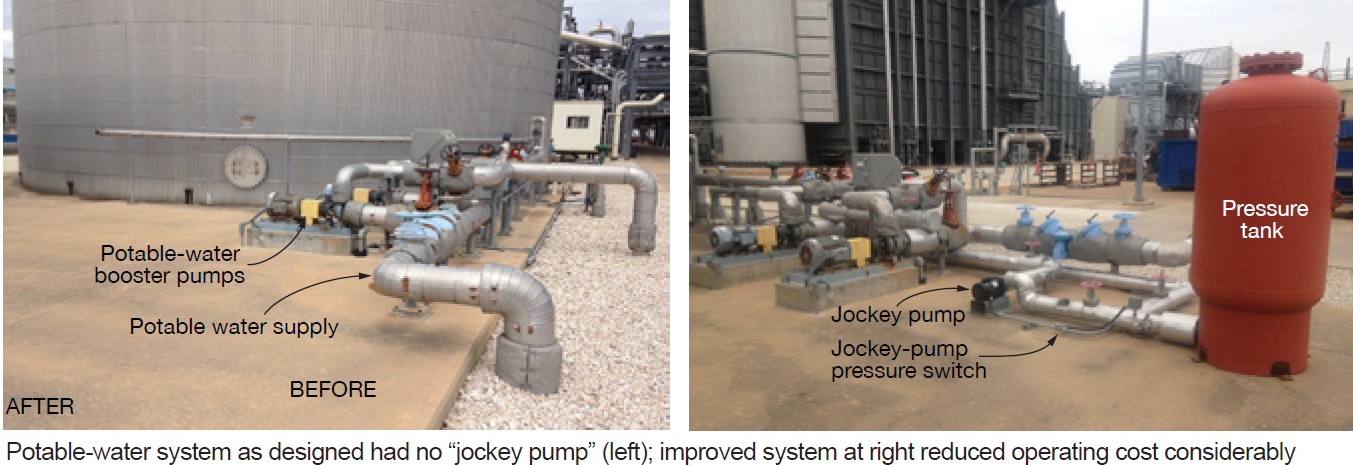
Staff changed the DCS logic for the booster pumps such that as pressure drops (as when the demineralizer is placed in service and the jockey pump cannot keep up with demand), a booster pump will start. Since its discharge pressure is higher than the jockey pump’s “on” pressure, the jockey pump turns off. When the flow requirement for the demineralizer drops below the 27 gpm minimum flow level, the booster pump shuts down and the system returns to jockey-pump pressure control.
In the year prior to this modification, one booster ran continuously, logging 8760 hours. In the year following, a booster pump was in service for only 2520 hours. This difference calculates to 10.1 million gallons of potable water reduction for a saving of $40,435.
An additional saving of $3592 in the cost of power to operate the jockey pump versus the booster pump is offset by the added cost of chemically treating the river water of $3,380. This yields an approximate annual saving of $41,000. The total cost of installation, including materials and labor, was $39,836, which gives the 550-MW, 2 × 1 combined cycle a one-year payback.
Project participants: Most of the design work for this project was performed by a team of four engineering interns from a local university working with several members of the plant staff. The installation was a staff effort.
Hinged access panels provide easier access to/escape from GT accessory module
Gaining access to some sections of the gas-turbine accessory module were difficult at MEAG (Municipal Electric Authority of Georgia) Wansley Unit 9, operated by NAES Corp. Areas technicians had to enter to monitor vibration and perform other routine maintenance on the two gas turbines at this 520-MW combined-cycle plant could be a tight squeeze—a safety concern if a fire were to start with someone inside or if the CO2 system discharged accidentally.
Even with a mandated warning system and time delay, escaping in timely fashion could be difficult. The red arrow in Fig 1 shows one of these locations: clearly there’s very little room to move freely, and the access panels would take time and effort to remove (Fig 2 left), making a quick exit challenging.
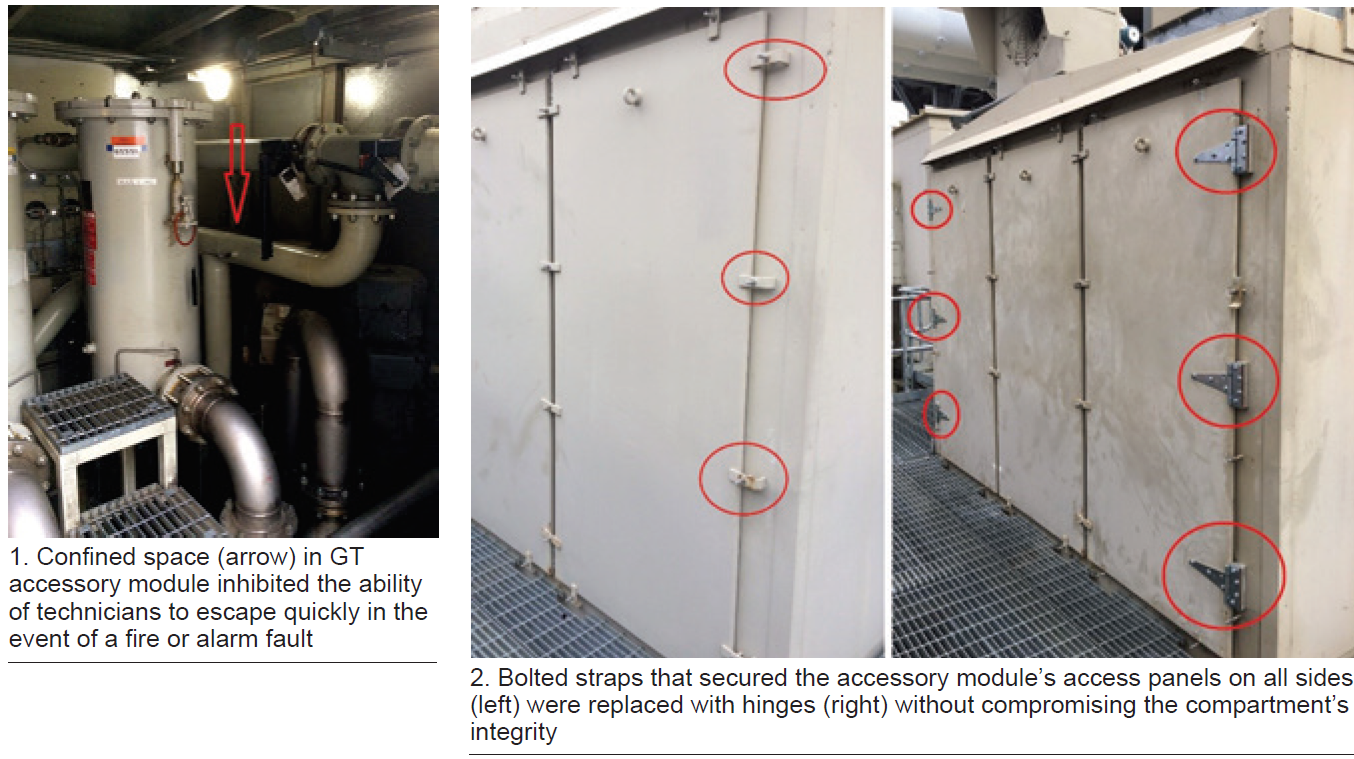
Plant personnel, led by Timothy Williams, considered equipping technicians entering the module with breathing packs. But they were concerned that their size might restrict movement and vision, and might not provide team members what they needed where and when they needed it. After further review, staff decided to improve access by installing hinges on the existing accessory panels (Fig 2 right), thereby converting them to access doors. The panels were hinged in a manner that assured the integrity of the accessory module would be retained.
The bottom line: At a tiny fraction of the cost of breathing packs, the solution described provides much easier and safer personnel access for regular maintenance. Plus, the doors eliminated concerns regarding escape from a confined space.
Corrective action, ergonomic improvement for GT offline water-wash drain valves
Some offline water-wash drain valves are difficult to operate when new and become nearly impossible to operate after a few months in service. This creates a significant ergonomic risk of muscle strain or sprain and fatigue for the operator tasked with aligning this valve for compressor cleaning.
If the valve is not fully closed, or is over-closed past the stops (which causes the same condition as a valve not being fully closed), there are possible safety and equipment risks as well. When the unit is placed back in operation, hot air from the compressor discharge case and combustion gases will pass through the carbon steel drain header, causing it to heat up enough to burn off paint.
Personnel at MEAG (Municipal Electric Authority of Georgia) Wansley Unit 9 conducted a root cause analysis that included the full disassembly of an existing stuck valve on one of the 520-MW combined cycle’s gas turbines. Facility is operated by NAES Corp; plant manager is Timothy Williams.
The RCA found severe rust accumulation inside the cast-carbon-steel valve body and a broken valve-closed stop. The rust had accumulated between the ball (Type 316 stainless steel) and seat, and rust was compacted between the ball and body, under the seat rings and in the stem (also Type 316) packing area as well.
The primary root cause: Corrosion of the valve body over time and jamming the seats against the ball and the stem in the body. Investigators found that the corrosion was caused by water—from the wash activity and condensation from normal operation—contacting the valve’s cast carbon steel body.
The “unidirectional” design of this particular ball valve uses system pressure to force it against the downstream seat, leaving the upstream seat lightly loaded. This may allow moist compressed air to condense in the header over time and infiltrate the valve body, aggravating the corrosion problem.
A special overhaul kit was ordered from the vendor of the non-standard valve, which was specified by the OEM. The valve was completely disassembled, grit-blasted to remove rust, and visually inspected for pitting and other damage. Staff then applied a high-heat-resistant spray-paint coating (one that did not require an oven-curing process) on the inside and outside of the valve body—except for the stem packing seal area, which was masked for protection.
The valve was reassembled with new seat rings and gaskets and all fasteners were torqued according to the manufacturer’s published procedure. As an added ergonomic benefit, the original brute-force valve operator (photo, left) was replaced with a gearbox operator and handwheel (photo, right).
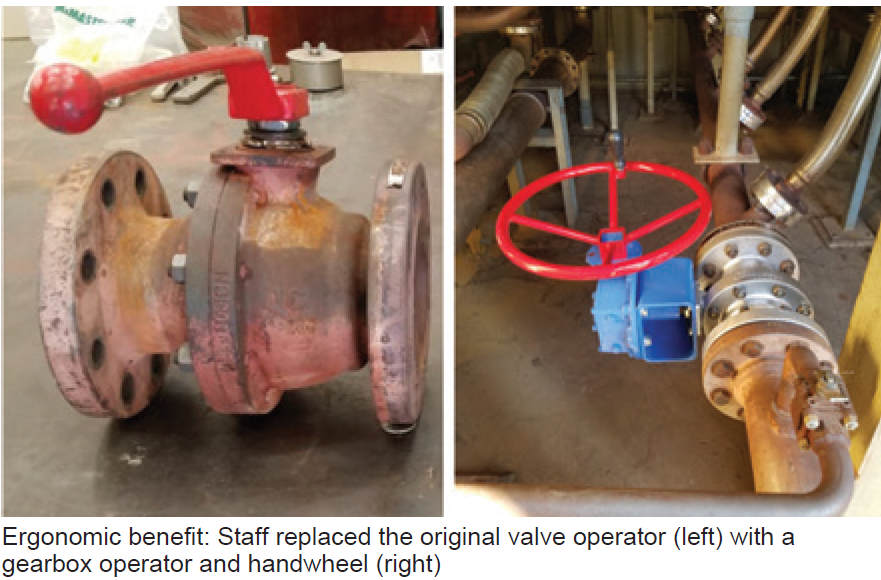
After more than six months of operation, the valves were still easy to operate and showed no signs of leak-by. The new gearbox operator and handwheel mitigate any risk of strain or sprain for technicians.
Mobile backup battery bank streamlines discharge testing
Hugo Ordoñez Ruiz and his team at Nuevo Pemex Cogen (Villahermosa, Tabasco, Mexico), operated by NAES Corp, wanted to identify a means for reliably performing battery discharge testing as stipulated by IEEE, as well as by NERC standard PRC-005-02, at the recommended intervals without jeopardizing the integrity of facility operations. The plant produces 277 MW and 1.76 million lb/hr of steam with its two gas-fired 7F/single-pressure HRSG trains.
Nuevo Pemex currently has 10 battery banks:
-
- Two rated 125 V dc/1300 AH for dc distribution system A/B.
- One 125 V dc/1500 AH for main UPS.
- One 125 V dc/600 AH for secondary UPS.
- Two 125 V dc/600 AH for dc systems for the gas turbine controls.
- Three 125 V dc/300 AH for the electrical S/S.
- One 125 V dc/190 AH in the ERM (European Reference Materials) for fuel gas.
Battery banks provide the ultimate defense against a possible catastrophe. For example, backup dc power assures a continuous supply of lube oil to the turbine bearings in the unlikely event ac power is lost.
Recall that battery capacity can decrease significantly before reaching the storage device’s design lifetime. High ambient temperature, dust, loose contacts, overload, and other conditions all take their toll. Periodic discharge testing is the only reliable way to measure capacity over time. However, if testing were conducted during routine operations, the battery bank would be disabled for a brief period, leaving the system unprotected by its backup power.
Battery banks typically are not designed with built-in redundant systems, and it would require a huge investment to retrofit each of the plant’s 10 existing banks with its own backup unit.
Plant staff collaborated and came up with the idea of building a mobile backup battery bank that would provide redundant power while discharge-testing each battery bank—rather than taking the plant offline or waiting until the next planned outage.
Capacity of the mobile bank was based on the highest “real” consumers among all of the installed banks (allowing for the fact that some of the banks are oversized). Staff determined that a 125-V dc/600-AH bank would serve the purpose.
A 19 × 7 × 8-ft metal shipping container was selected to house the batteries. The mobile bank is divided in two sections: one holds the rack of 60 SBS 900 batteries that make up the 125-V dc/600-AH bank, the other the charger (figure).
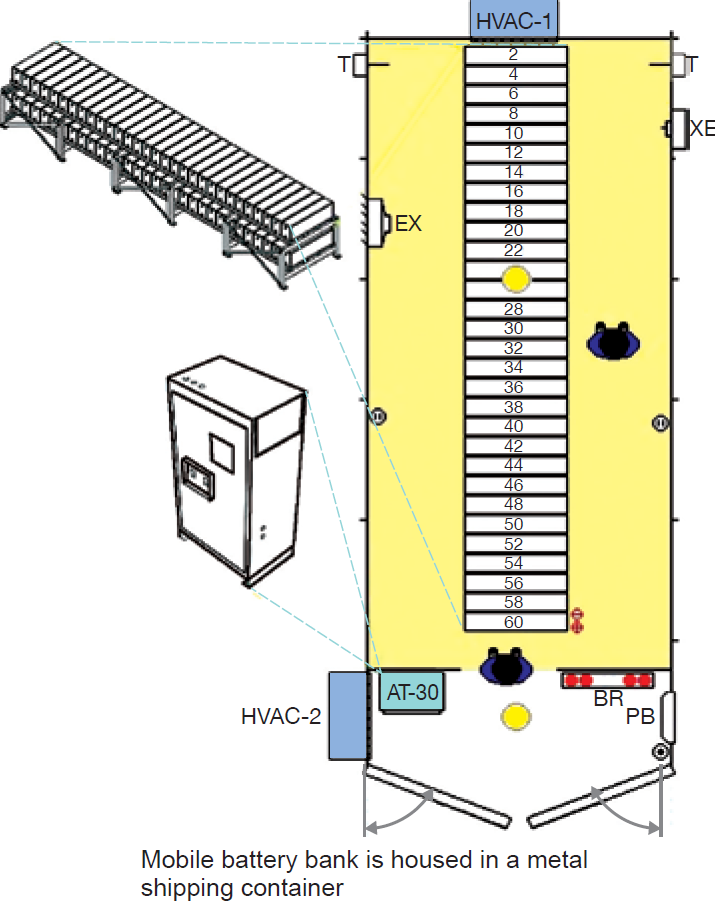
The shaded zone in the drawing is equipped with lighting, accessories, HVAC, and instrumentation that meet Class 1, Division 2, explosion-proof requirements. HVAC-1 is a 24,000-Btu/hr heating/cooling unit; the Ts are local temperature gauges; XE is a stand-alone gas monitor with highly visible LED indicators, piezo horn, and strobe lamp. EX is a 12-in. vertical extractor activated automatically by the XE to extract explosive gases from the enclosure.
The unshaded zone at the bottom of the figure houses an AT-30 CPU-controlled battery charger; a distribution panel (PB) that feeds all of the installed equipment; and HVAC-2, a non-explosion-proof 12,000-Btu/hr heating/cooling unit.
Bulkhead pass-through ports reduce safety hazards, extend equipment service life
During outages and other activities, plant and/or contractor personnel may have to pass hoses and electrical extension cords out of the enclosed power block to service containers, trailers, or auxiliary air compressors. When they are passed through doorways or rollup doors, a trip or overhead hazard is created; plus, electrical-cord insulation can be damaged.
To mitigate these risks, the empowered staff at Rathdrum Power Plant, a 275-MW 1 × 1 combined cycle owned by Tyr Energy and operated by NAES Corp, came up with the idea of creating pass-through ports in the exterior bulkhead adjacent to high-use pedestrian and vehicular access doors. Simple enough. First step is to use a hole saw to “drill” holes. Next, insert lengths of PVC pipe through the holes and plug the ends of the pipe with PVC caps. When ports are needed, merely remove the caps and pass the hose or cord through pipe. In addition to eliminating safety hazards and clutter, the pass-through pipe extends the service lives of hoses and chords.
Plant Manager Gary Allard’s team also cut ports into the gas-turbine combustion compartment, thereby allowing an explosion meter to run verification checks in the event a “high combustibles” alarm is received. The same pass-throughs also can be used to verify compartment atmosphere is safe for employee access.
The two safety enhancements were inspired by Rathdrum’s continuous improvement program and its efforts as a VPP Star plant to actively pursue safety improvement opportunities.