Cogen plant reduces energy cost, emissions while improving service reliability
Timely permitting, financing, and construction of public-works projects generally are difficult goals to achieve in the nation’s most populous state. Competing interests, public skepticism, lack of money, and plain old politics militate against building just about anything in California. Even projects that make good sense, like cogeneration plants can drag on for years. The Orange County Cogeneration Plant is a case in point.
Gus Fisher, today manager of facilities operations for the county, was a young engineer in the mid 1980s when he and colleagues at the Central Utility Facility (CUF) in Santa Ana proposed building a cogeneration plant to serve the surrounding Civic Center Campus. By way of background, the CUF was built in 1968 to provide steam and chilled water to the many city, county, state, and federal buildings on the sprawling campus. Electricity was supplied by Southern California Edison Co (SCE).
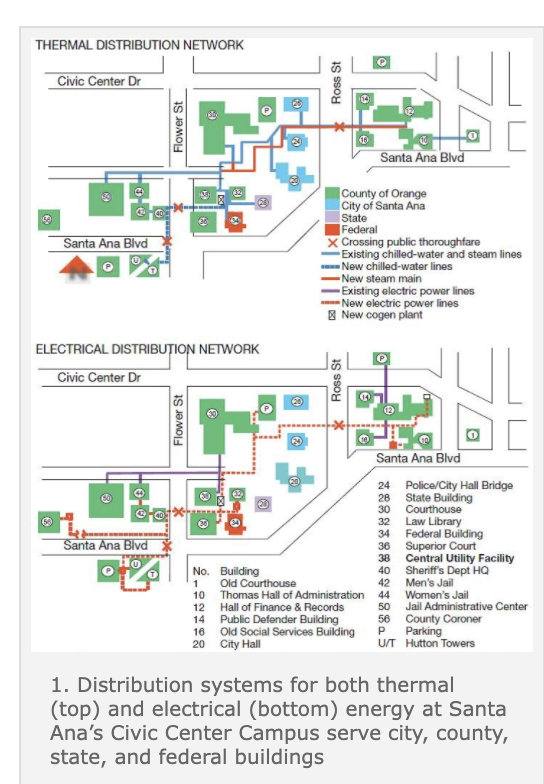
Fischer and his co-workers never gave up on the idea and their perseverance paid off-albeit a quarter of a century later–when the cogen plant began operating in November 2009, powered by two 5.2-MW Taurus 60 gas turbines from Solar Turbines Inc, San Diego. Steam is produced by supplementary-fired heat-recovery steam generators (HRSGs), supplied by Rentech Boiler Systems Inc, Abilene. The boilers are each rated 28,000 lb/hr at 265 psig with the turbines at maximum output and duct burners off.
In the end, the “makes good economic sense” argument for building the plant in the mid 1980s was not what moved the project forward, Barbara Tidball, senior project manager for Orange County Public Works, told the editors. Although economics was important, she said, the key drivers were reliability and “green” initiatives.
Californians hadn’t forgotten the state’s electricity crisis at the beginning of the millennium and grid independence was high on the agendas of project supporters. The cogen plant also was viewed as the cornerstone of the county’s efforts to reduce its carbond footprint. Emissions from teh facility’s gas turbines would be only a fraction of those from the CUF’s steam boilers. Plus, the initiative provided the opportunity to modernize campus-wide energy distribution systems and upgrade office buildings to green standards.
Energy distribution. The underground thermal and electrical distribution networks for the Civic Center Campus are described in Fib 1. San Diego-based Rick Lyons, PE, VP of Syska Hennessy Group Inc’s Energy Services organization, the engineer/project manager for the infrastructure upgrade and cogen project, and colleague Al Ribaudo, director of energy services, told the editors that installation of piping and electrical cable had its challenges.
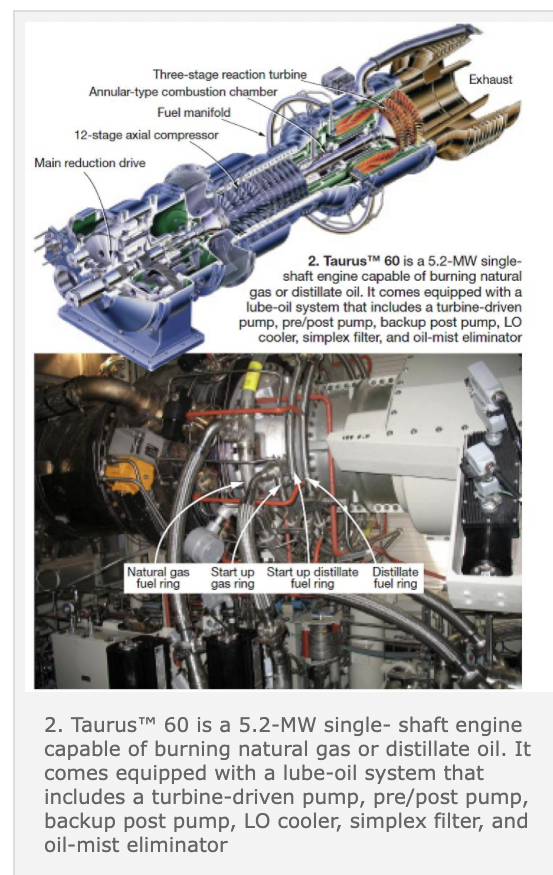
For example, Syska had to jack and bore across several four-lane roads while adhering to very strict requirements on street interruption. Also the new distribution cable and steam piping had to be installed without disturbing water and sewer lines and other underground infrastructure.
Most of the campus buildings were built between the mid 1950s and the early 1970s, and some steam mains did not pass infrastructure evaluations for continued use long-term. By contrast, the chilled-water piping was in good condition and was retained. The original steam lines were abandoned in place and a new Perma-Pipe grid was installed throughout the campus. Pipe rests on a bed of sand within a trench which also accommodates the electric distribution cable. Steam sendout is at 85 psig; pressure is reduced to 20 psig at the campus buildings using pressure reducing valves.
Perma-Pipe Inc, Niles, IL, manufactured the pre-insulated pipe, which is protected by an outer steel jacket of 22-guage thickness. Both steam send-out and condensate return piping share the insulated space within the jacket. Diameter of the steam piping is 6, 8, or 12 in., depending on its locating on the grid.
A special permit was granted to burn distillate to mitigate reliability issues. The turbines can reach rated output on Amber 363, an ultra-low-sulfur oil (less than 1 ppm) which was developed as a standby fuel with the emissions requirements of California’s South Coast Air Quality Management District Regulation 1146 in mind. HRSG duct burners are capable of firing only natural gas. The Rentech HRSGs are equipped with CO catalyst beds and SCRs to restrict NOx emissions to 2 ppm. Physical constraints on boiler length forced engineers to rely on vertical-flow SCRs and economizers (Figs 4-6). The CO catalyst is in the evaporator section and not shown on any of the drawings.
Operational Flexibility is provided by a sophisticated control system that enables the gas turbines to closely follow load, and by two dump condensers (one per GT/HRSG train) located on the plant roof, each capable of condensing the unfired steam output of a boiler (Fig 7.) The cooling towers that support the chillers also are the source of cooling water for the dump condensers. Fine-tuning of plant operations was the primary goal of Tim Corbett, manager of plant operations, for 2010.
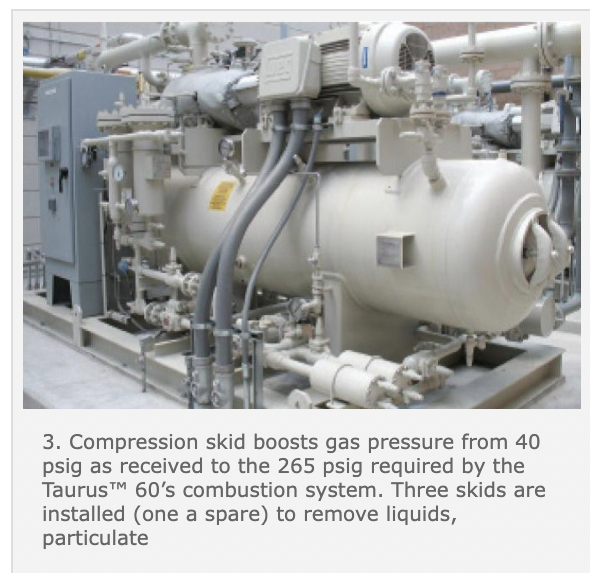
End notes: environmental. In addition to reducing CO and NOx emissions to state of the art levels, the plant’s noise profile did not increase with the addition of the gas turbines, HRSGs, and system auxiliaries. Scenic vistas were maintained by use of appropriate architectural curtains to block from view rooftop equipment (Fig 8).
Energy conservation. Lighting load in the cogen plant was minimized by use of skylights (Fig 9). Conservation efforts in campus buildings have had a significant positive impact. Energy management systems have been upgraded to today’s standards, all controls on air handling units have been upgraded or replaced, operation of heat exchangers (plate type and shell and tube) used to make hot water for climate control and domestic purposes has been automated, etc.
The original electric distribution system delivered 12-kV power supplied by SCE to all buildings. Utility transformers at each location dropped the 12 kV to 4.16kV and power delivery was metered. Those transformers were removed at county buildings and replaced by 4160 to 480 V transformers supplied by Eaton Corp. The high-side voltage on the Eaton transformers is the same as that at the generator terminals. Note in Fig 1 that the cogen plant supplies electricity only to county buildings but provides thermal energy to all buildings. The gas turbines are sized to handle the county’s peak campus load, based on records provided by SCE. A 10-MW 12 to 4.16 kV transformer was purchased by the county to fully back up the gas turbine/generators in the event of an outage. Reliable utility services are necessary 24/7 because of the two prisons located on campus.
Peak electric demand currently is 8.1 MW and the peak steam requirement 65,000 lb/hr–numbers unlikely to increase anytime soon because of the economic downturn. The current interconnection agreement requires the county to import a minimum amount of electricity to prevent islanding. The next agreement will permit export.
The dual-fuel Taurus 60s feature a 12-stage axial compressor with a 12.2:1 pressure ratio; the reaction-type turbine has three stages (Fig 2). Generator is a wye-connected synchronous machine with a brushless exciter. Chiller coils in the air inlet houses allow the gas turbines to maintain rated output year-round; water for the coils comes from the campus chilled water system. The CUF is home to three steam-turbine-driven centrifugal chillers (900, 1300, and 2000 tons) and two absorption units rated 1200 tons each. Primary fuel is natural gas, which is supplied at about 40 psig and boosted to the GT requirement of 265 psig with a prepackaged onsite compression system equipped to remove both entrained liquids and particulates (Fig 3). Three gas pretreatment skids are installed–one per engine and a spare. A supplementary gas line has to be installed at the plant to accommodate the gas turbines.
A special permit was granted to burn distillate to mitigate reliability issues. The turbines can reach rated output on Amber 363, an ultra-low-sulfur oil (less than 1 ppm) which was developed as a standby fuel with the emissions requirements of California’s South Coast Air Quality Management District Regulation 1146 in mind. HRSG duct burners are capable of firing only natural gas. The Rentech HRSGs are equipped with CO catalyst beds and SCRs to restrict NOx emissions to 2 ppm. Physical constraints on boiler length forced engineers to rely on vertical-flow SCRs and economizers (Figs 4-6). The CO catalyst is in the evaporator section and not shown on any of the drawings.
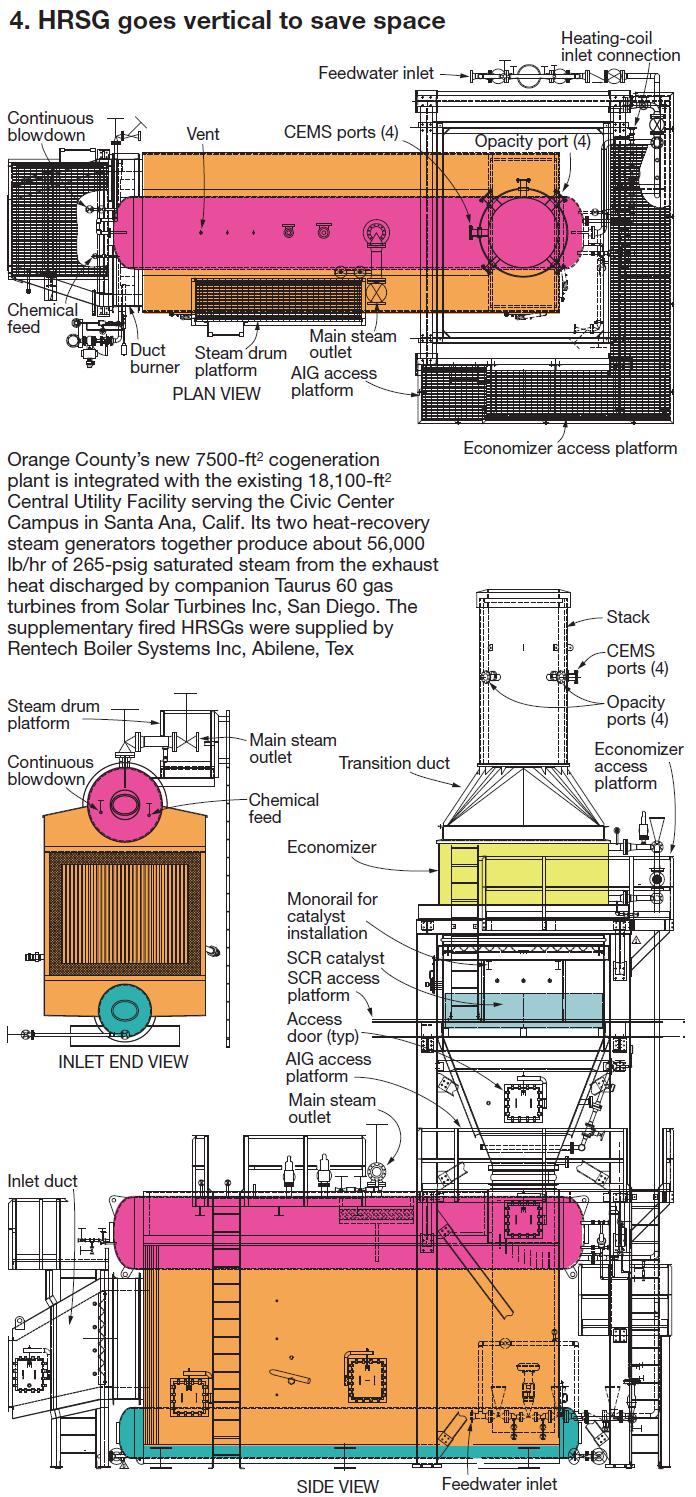
Operational flexibility is provided by a sophisticated control system that enables the gas turbines to closely follow load, and by two dump condensers (one per GT/HRSG train) located on the plant roof, each capable of condensing the unfired steam output of a boiler (Fig 7). The cooling towers that support the chillers also are the source of cooling water for the dump condensers. Fine-tuning of plant operations was the primary goal of Tim Corbett, manager of plant operations, for 2010.
End notes: environmental. In addition to reducing CO and NOx emissions to state-of-the-art levels, the plant’s noise profile did not increase with the addition of the gas turbines, HRSGs, and system auxiliaries. Scenic vistas were maintained by use of appropriate architectural curtains to block from view rooftop equipment (Fig 8).rhe dump condensers. Fine-tuning of plant operations was the primary goal of Tim Corbett, manager of plant operations, for 2010.
Energy conservation. Lighting load in the cogen plant was minimized by use of skylights (Fig 9). Conservation efforts in campus buildings have had a significant positive impact. Energy management systems have been upgraded to today’s standards, all controls on air handling units have been upgraded or replaced, operation of heat exchangers (plate type and shell and tube) used to make hot water for climate control and domestic purposes has been automated, etc.
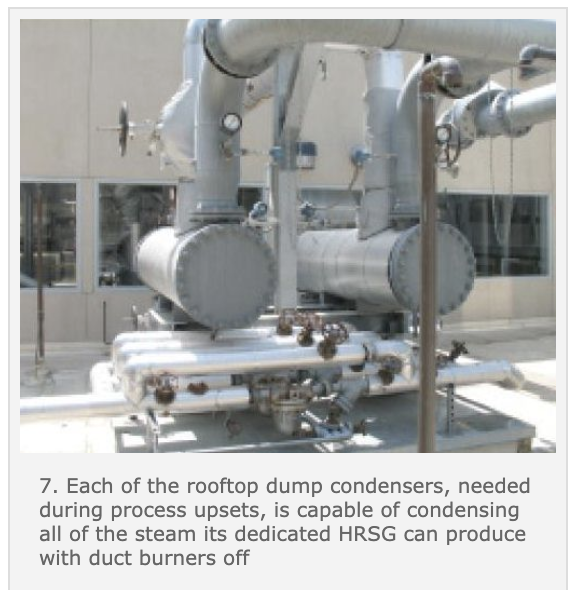
