Tenaska Virginia Generating Station - Tenaska Virginia Partners LP
Challenge. Our on-going challenge is to obtain “buy-in” into our safety culture from the on-site contracted employees, and ensure contractors understand the facility’s safety policies and partner in our safety culture.
Solution. We maintain and strengthen our safety culture by utilizing every employee and contractor’s opinion to maintain a safe worksite. The following are some components used to develop our contractor safety relationships:
- All employees are open and eager to learn from best practices, safety experiences, and lessons learned. The staff exhibits a positive attitude, integrity, and they are always looking to identify, track, and correct safety deficiencies.
- Our annual contractor 45-minute safety brief and exam were translated into Spanish. A written exam is given at the completion of training to test retention of presented information. A grade of 100% is required to pass the exam and work at the facility.
- Crucial to achieving contract employee “buy-in” in our safety culture is building trusting and helping relationships. Employees and contractors work together to perform detailed job hazard analysis and LOTO system walk-downs.
- We work with the contractor to determine the best method for execution of a job. We ensure that contractors know their opinion counts. Each contractor job has a facility team member assigned to be their main point of contact.
- All outage work permits, hot work, scaffolding, and confined spaces are posted in the control room so everyone knows what jobs are in progress.
- A safety toolbox meeting occurs every Wednesday morning during our maintenance outage in the control room. Safety issues identified are discussed with all plant personnel, contract supervisors, and their employees.
- An outage safety barbecue is held with all contractors and employees to express the importance of following our safety policies, sharing safety ideas, and understanding our commitment to safety and esprit de corps.
- A safety traffic stop light is mounted in the control room (Fig 1). A green light represents no safety near misses or missed opportunities. A yellow light indicates a near miss. A red light indicates an accident or hazardous situation.
- Contractor supervisors and all employees are required to sign our team safety charter (Fig 2). This ensures we are all on board in maintaining an open honest safety culture.
- Contractors are scheduled to provide employee training on complex maintenance tasks such as setting up and inspecting scaffolding and valve maintenance.
- A safety stand-down has been used in the past when an employee believed there was an unsafe maintenance practice. All facility maintenance stops and a brief is conducted with those involved.
- Every year the facility decides on “Contractor of the Year” and a special award is presented to the contractor during lunch.
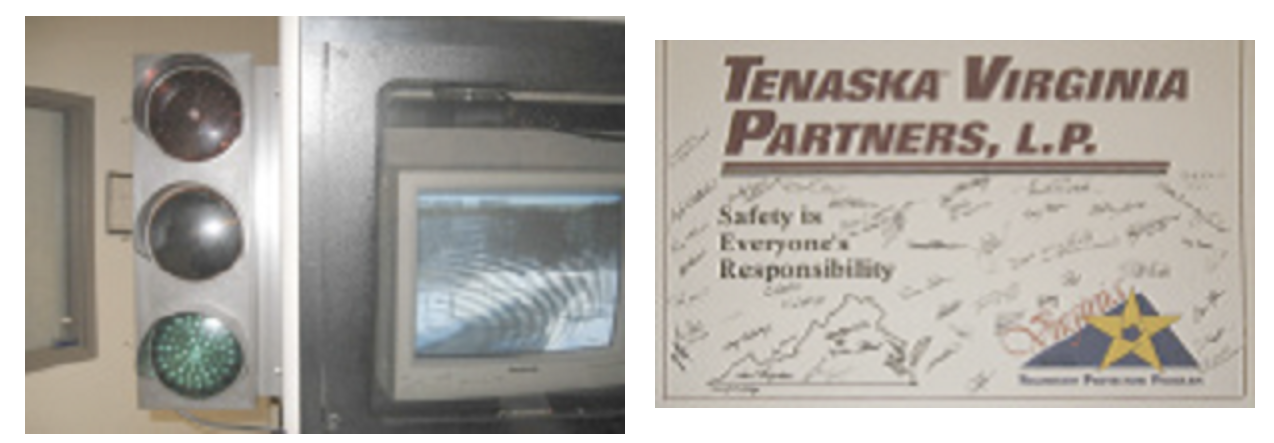
Results. Contractors know they can bring up safety concerns/issues and their opinions are important to improve our safety culture. OSHA VPP benchmarked our contractor safety brief process. We know we are doing it correctly when contractors, who work with companies all over the world, take time to walk up to us before they leave facility to say “thank you,” shake your hand, and tell us how much they enjoyed working with the team.