Superstorm Sandy was one of those events which changed most everyone’s thinking on infrastructure reliability, especially in the NYC metropolitan area. But Sandy is only one element in the “perfect storm” which led Montclair (NJ) State Univ (MSU) to add a microgrid to its relatively modern combined heat and power (CHP) system.
Other elements include a unique state-level public/private partnership created in 2009 in the wake of the “Great Recession,” recurring utility-side events responsible for several campus-wide outages annually, and ratcheting utility demand and T&D charges.
Today, MSU can operate 100% divorced from the grid and export up to 3 MW of power to it, thanks to an engine-based 5.2-MW microgrid commissioned in May 2018 that works in tandem with a 5.6-MW gas-turbine/HRSG-based combined heat and power facility commissioned in 2013 to replace and upgrade an antiquated CHP system installed in the 1950s. The gas-fired engines can also burn LNG, for yet another level of backup.
The two 2.6-MW Jenbacher engine/gen sets anchoring the microgrid have three functions, according to Plant Manager Andrew Morrissey: peak-demand shaving, backup capacity when the gas turbine is in an outage, and supplemental generation when utility power supply is lost. On a normal day outside of the peak season, however, MSU “sells a little power to the utility during nighttime, and buys a little power during the day,” adds Morrissey.
The CHP plant can deliver 100% of the campus steam and cooling needs and up to 86% of its electric demand. But recurring issues with utility-supplied power caused MSU to invest in further relief, the microgrid.
In a presentation to the Distributed Energy Conference, Denver, October 2018, Frank DiCola, CEO of DCO Energy LLC, noted that, over its first summer, the new microgrid netted close to $400,000 in savings by shaving electric demand peaks. “Utility capacity charges were the main economic driver for the microgrid project,” he said. Electricity costs to MSU are now 40% lower than before the new CHP.
Jonathan Wohl, DCO’s senior VP of project development, noted during CCJ’s visit to the facility, that the T&D cost component of MSU’s utility bill is also rising significantly, as the utility adds T&D infrastructure to bring in more renewable energy. Of course, what will also happen is that as more customers like MSU divorce from the grid to the extent possible, costs for maintaining the “grid” have to be spread among fewer customers and/or customers buying fewer kilowatt-hours.
Another project driver was the reliability of grid-supplied electricity. MSU could experience as many as three blackouts a year, even though there are two 26-kV utility lines feeding the campus. Disturbances on the utility lines could also trip the turbine in the old CHP plant. Outages typically were from 30 minutes to several hours in duration. Superstorm Sandy in 2012 added to the concern about resiliency of campus utilities.
Risk mitigation and resiliency run deep in the psyche of the facility staff. DCO, which develops, designs, builds, operates, and maintains CHP systems across the country, has engine, turbine, and chiller expertise groups within the firm. The process performance group identifies cross-facility issues and addresses them. At MSU, spares are carried for any component with over a 10-week delivery time.
“We evaluate the N+1 risk for all major components across our fleet,” said Fred Eckert, DCO’s executive VP of facility operations. Morrissey referred to a fuel splitter valve for the gas turbine with a 52-week lead time. “I keep one of these in my office,” he said, pointing to it on the floor in the corner.
Since the gas turbine doesn’t run without it, the HRSG is a major risk component because it can take down the turbine. All of the campus steam normally is provided by the 28,000-lb/hr HRSG (at baseload), equipped with a duct burner capable of producing an additional 22,000 lb/hr. Two backup fired boilers, each rated 42,000 lb/hr of steam, also are available; one is kept in hot standby at all times.
Two large chillers are used for cooling; one (2300 tons) is steam-turbine driven, which also adds a large “sink” for productive use of steam when electric demand is high and campus steam demand is low. This is important because the system does not include an HRSG bypass stack. The other chiller is a 2000-ton motor-driven unit. Both chillers were supplied by York®, a unit of Johnson Controls.
A big challenge for the CHP construction team was trenching through solid rock to add 8500 ft of condensate return lines. That caused a hit on the budget, although the overall project remained within anticipated costs. The antiquated CHP system was only returning 20% of the condensate. “It returned more rainwater than condensate,” quipped Eckert. As the campus grew, chilled-water demand kept growing. MSU had resorted to renting chillers for individual buildings. Today, 90% of the condensate is returned; DCO has a contract guarantee at 80%.
A lesser challenge on the O&M side proved to be raw-water quality for the boilers. The campus buys water from the city, but it often has to be supplemented with well water. When that happens, “the hardness goes through the roof,” said Morrissey. Adding deionizer resin bottles brought the issue under control.
Like most powerplants these days, the CHP + microgrid is controlled with a sophisticated SCADA system. MSU’s includes a Rockwell Automation system with Schweitzer Engineering Laboratories’ relays and load-management system (LMS), the last incorporating model-predictive control. The controller adjusts actual electrical, steam, and chilled-water loads versus what is expected based on ambient conditions (temperature and humidity) and historical demand data.
A dispatch model crunches real-time LMP pricing data from PJM (figure) and electricity costs to MSU to determine whether to sell or buy and how much. Recall that LMP is the acronym for “locational marginal pricing.” To establish the predictive model, DCO reviewed historical 15-min demand intervals to “predict” when and how much peak-shave electricity would be needed from the microgrid engines. The engines are only permitted to run 2000 hours per year.
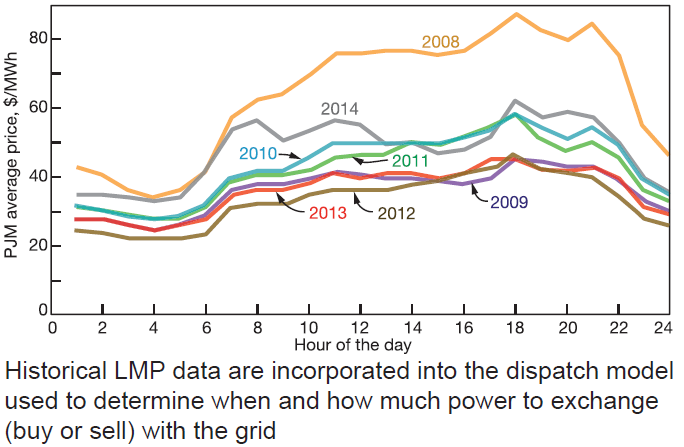
There can be significant and unanticipated electric demand from the campus. For example, electric demand tends to spike during rainy days. Although classes are typically not in session during the summer, there are many special events and the CHP + microgrid facility operators may not get much notice about when they are occurring.
The LMS controls every major electrical breaker on the campus, and also is tied into a load-shedding strategy when necessary. Overriding objective is to avoid ratchets on the utility demand charges, which are calculated based on the five single hours of highest demand in the current year setting the rates for the following year. According to DiCola, historical data showed that the highest demand hours occur during the third weekday of heat waves characterized by 90F+ temperatures and high humidity. Black-start capability also is built into the LMS.
No money down. The state public/private partnership program allowed MSU to add the CHP facility with no capital investment. A 2009 Economic Stimulus Program encouraged universities and others to take advantage of public private/partnerships combining taxable and tax-exempt bonds to finance facilities over 30 years. DCO was awarded both the EPC contract and a 30-yr O&M contract.
As part of that, the major equipment, primarily the gas turbine/generator, engine/generators, and motor- and steam-turbine-driven chillers, had to be protected by long-term service agreements.
MSU decided to take advantage of the program and modernized the existing CHP—consisting of two legacy boilers, a 1950s-vintage steam-distribution and condensate-return piping network, a 1990s-vintage Solar Turbines’ Centaur 40 gas turbine/generator coupled to an HRSG from the same time period, a small black-start engine/gen set, and backup generators “past their prime” in several buildings.
The central plant was operating at an efficiency of less than 50%, reported DiCola. There was no chilled-water distribution network, only local rental chillers. The entire steam distribution system had to be replaced. These and other deficiencies were delineated in a 2009 Energy Master Plan issued by MSU.
MSU’s facility was the first powerplant under the stimulus program. The CHP + microgrid is expected to save $2-million annually, including debt service. The facility also received a clean energy grant from the state EPA. The GT emits only 9 ppm of NOx, thanks to Solar’s SoLoNOx emissions reduction technology, which requires no reagent and no water or steam injection. The plant was not required to include continuous emissions monitors.
CHP plant availability reported by DiCola in his presentation was 97.4%. “Most of our issues are with the utility, not the onsite equipment,” Morrissey said during the site visit.
Capital, always scarcer than one wishes, could now be put to work towards MSU’s primary mission, educating students and expanding campus facilities. The college campus is New Jersey’s second largest, with 27,000 students, 8000 in the dormitories. Indeed, the campus continues to grow, adding buildings and refurbishing older ones.
As importantly, MSU is relieved of the responsibility for day-to-day deliveries of critical energy streams, and can focus on monitoring consumption to identify and address inefficiencies. DCO also manages fuel supply for the university, which can be dicey in the Northeast given harsh winters and bottlenecks in regional natural gas supply.
Certainly not a household name in the CCJ community, DCO Energy, headquartered in Mays Landing, NJ, employs close to 500 people and designs, builds, and operates CHP, cogeneration, small power, and non-utility powerplants across North America. According to DiCola, the firm is now in the process of evaluating the economics of battery storage at many of its facilities, which could be the final piece of the puzzle for sites wishing to divorce completely from the local utility.