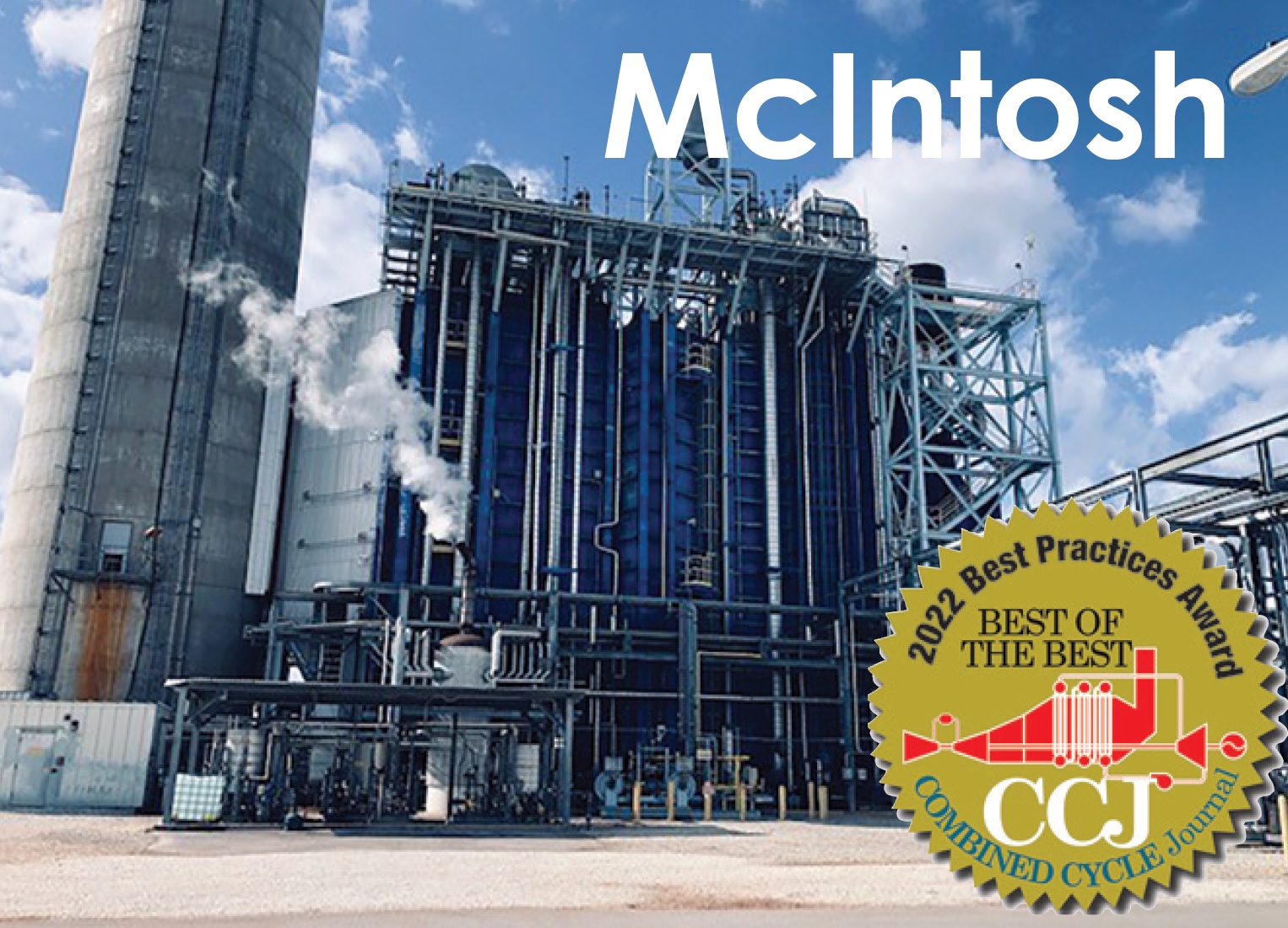
A challenge plant staff faced was how to monitor the steam turbine/generator to determine proactively if repairs are needed.
To ensure the Unit 5 steam turbine is available when the combined cycle must operate, Lakeland Electric (LE) personnel focus on preventive-maintenance activities to avoid a failure. The steamer is monitored continuously for backpressure on the L-0 blades (especially during shutdowns) and those airfoils are inspected for potential inclusions, and erosion (Fig 7) and tunneling, during operation.
On large steam turbines, the LP section’s L-0 blades can experience cracking because of off-specification operation, including excessive backpressure from the condenser—especially during a shutdown event. Thus, the utility has instituted continuous monitoring of backpressure on the steam turbine that initiates an alarm thusly:
- Offline—alarm at 4.5 in. Hg; trip at 5.5 in. Hg.
- Online—alarm at 7.0 in. Hg; trip at 8.0 in. Hg.
Additionally, the steam-jet hogger air ejector automatically comes into service if there is a steam-turbine trip—this to ensure backpressure is maintained.
To verify there are no inclusions in the L-0 blades (Fig 8), LE has instituted periodic inspections (annually at a minimum). The inspections are completed in situ by completing non-destructive examinations (NDE) of the blades. These inspections revealed that erosion was occurring at the trailing edges of the L-0 blades.
The inspections include visual and die-penetrant inspections, and molds are completed. All inspections are done in-situ from the steam-turbine hotwell to verify the potential for tunneling and/or cracking that may lead to a failure of the L-0 airfoils.
Use of continuous monitoring and NDE of L-0 steam-turbine blades have helped determine which ones are most susceptible to failure. These are the steps the utility has taken:
- Follow OEM recommendations regarding testing intervals—at a minimum.
- Conduct periodic in-situ NDE of the L-0 blades to ensure they can meet the desired service interval.
- Implement alarms to notify when a backpressure event may have occurred.
- Implement control logic to automatically put the hogger air ejector into service if there’s a potential for a backpressure event on the steam turbine.
The benefit of this activity, spearheaded by Scott Cox, NERC engineer, and Steve Reinhart, plant manager, is that the steam turbine continues to operate at desired service intervals.