Advanced single-layer turbine warming system
Pierre Ansmann and Norm Gagnon covered the basics of steam-turbine warming for increased startup flexibility in their breakout presentation, which began by answering the question, “Why install a turbine warming system?” Highlights of their PowerPoint, available on the Power Users website, include the following:
- Maintenance and operational benefits.
- Differences in warming-system arrangements.
- System durability and reliability.
- Importance of proper insulation for a warming system.
- Cost and schedule of the initial installation.
- Periodic maintenance plan.
In their review of alternative warming-system arrangements, the duo rejected those integrating heating circuits in insulation blankets, installing the heater on a thin mattress below the blanket, and using glass-fiber-insulated heating cable. The optimal system for the upper casing, they said, is a heater on a metal-mesh baffle; for the lower casing, permanent mounting of heating cable below the split line (Fig 7).
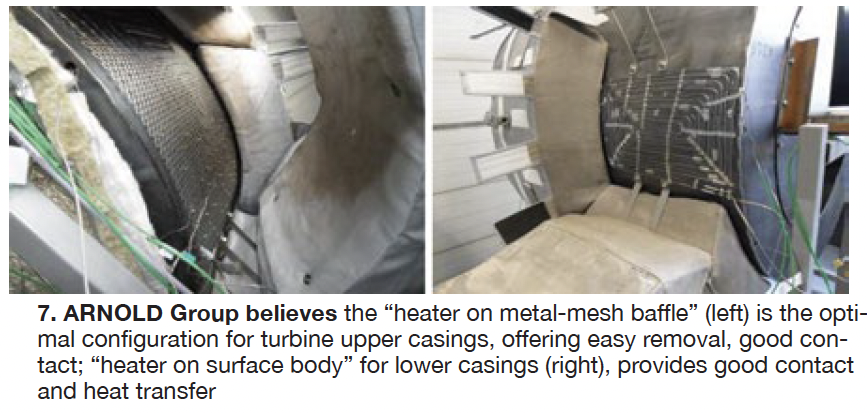
Ansmann and Gagnon explained that the ARNOLD system features interlocking high- performance blankets which conform perfectly to the turbine surface. High-quality materials and manufacturing, and long-term high-temperature resistance, allow the company to guarantee reuse of its insulation system for 15 outages without a decrease in efficiency.
More than five-dozen thermocouples, strategically located on the turbine, ensure proper heating. Each of the 18 or so heating zones has t/cs installed on the heating wires to double check if the zone is responding correctly and at the specified temperature. Below every heating zone, multiple t/cs are mounted on the casing to confirm even heating of the turbine.
The speakers said the ARNOLD warming system can maintain your turbine in a hot-start condition for at least four or five days after shutdown. No preheating of the turbine is required prior to a restart within this time period, reducing startup fuel consumption and auxiliary power.